Fireproof Assurance: Severn’s OCT TOV Butterfly Valves Exceptional Fire Safety Design and Testing Credentials
As part of a safety-first approach Severn incorporates into its innovative Oblique Cone Technology (OCT) Triple Offset (TOV) Butterfly valve, fire safety is a critical part of that safety first objective. Fire testing standards state the minimum requirements the valve must achieve in order to receive fire safe certification. The standards dictate the setup & parameters required to simulate the conditions a valve may be subjected to during a fire, and test to ensure the valve can operate satisfactorily afterwards.
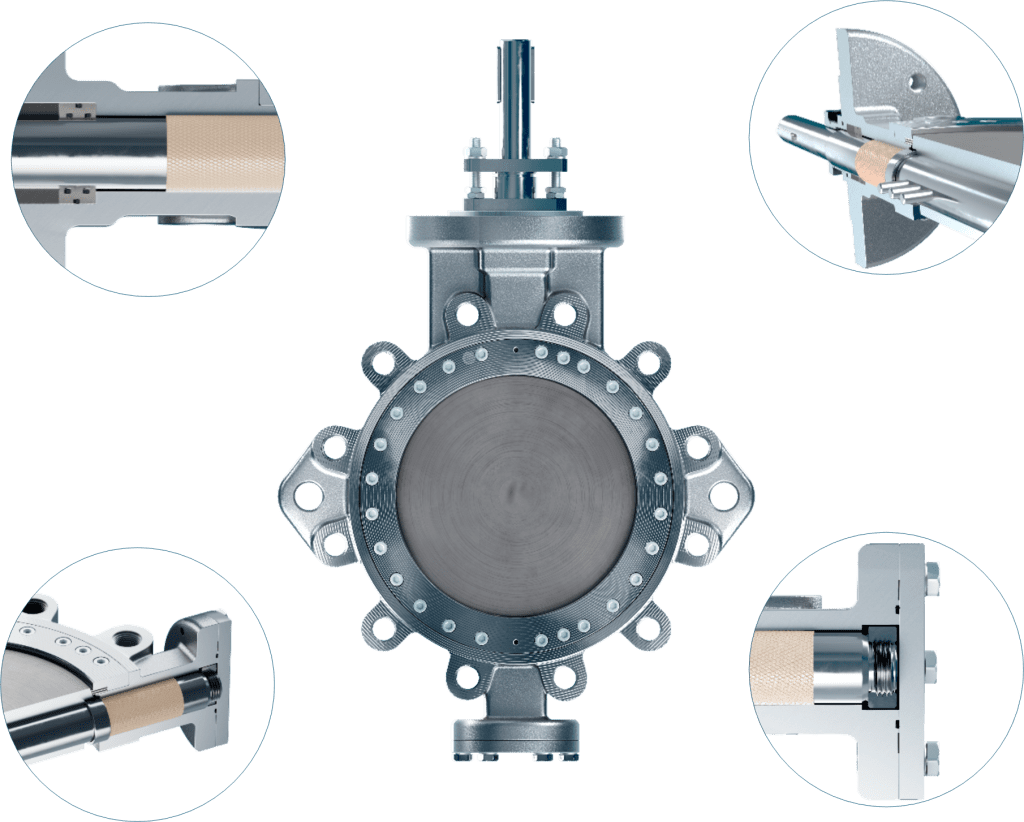
To summarise, the test consists of a valve being mounted in a fire test rig to flow water through the valve, and measure leakage both internally past the seal as well as externally through the packings and gaskets. The valves are then pressure tested at ambient temperature, once the valve has passed this element of the test, any leakage is recorded. The valve is then subject to a simulated fire by use of gas burners, with average temperatures of between 750°C & 1000°C recorded by thermocouples for the 30-minute burn time. Once complete, the flames are extinguished, and the valve is subjected to a forced cooldown using water to simulate the fire being extinguished on site.
The leakage during fire is measured and recorded. The valve is then subject to a re-ambient temperature and operational test, with the maximum leakage requirements being defined within the relevant standard. The tests are carried out in both the preferred and reverse directions and are witnessed by a 3rd party approval body to give added confidence that the valve will perform as required in either flow direction.
By investing in and developing their own on-site fire test facility, Severn can understand and interpret the results to re-design & develop the fire safe valve technology for the OCT TOV Butterfly Valve, to further exceed the requirements set out in the standard. By doing this, Severn have been able to achieve up to Zero seat leakage, even after fire testing, giving further confidence to the capabilities of the valves when installed and further ensuring safety first is achieved for the end user and their operations.
The key to Severn’s success lies in their patented Oblique Cone Technology (OCT), which received approval from the UK Intellectual Property Office in 2018. This innovative design uses an ‘infinite circle’ geometry that allowed the research and development team to develop the circular sealing geometry, which gives the flexibility to use the valve for both isolation and control duties with the option of interchangeable seals and control trims.
Utilising its over 60 years of engineering heritage, Severn have designed and developed the innovative OCT TOV Butterfly Valve, a valve that meets the requirements of API 6FA, API 607, and ISO 10497 fire testing standards. These bi-directional isolation & control valves offer repeatable zero leakage, providing peace of mind for operators while ensuring safety is at the forefront.
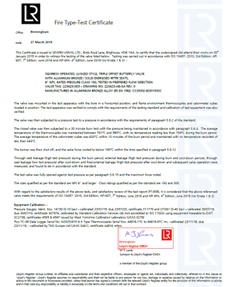
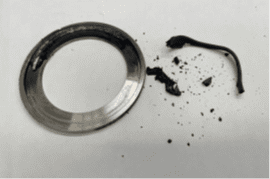
Severn’s certification for fire test covers the OCT Laminate, Hybrid (OCT-HS) and Seawater (OCT-SW) seals, achieving the required leakage rates in accordance with the relevant international standards. By designing, developing, and testing the hybrid seal (OCT-HS) Severn have been able to understand how the hybrid polymer metallic seal acts under extreme temperatures, which has enabled them to develop a graphite free, firesafe seal, that works even after being exposed to the extremes of a fire test. By using this knowledge, the OCT-SW utilises the hybrid seal technology and prevents any graphite from contacting with the line media, therefore on seawater service eliminates galvanic effects and extends the service life of the valve.
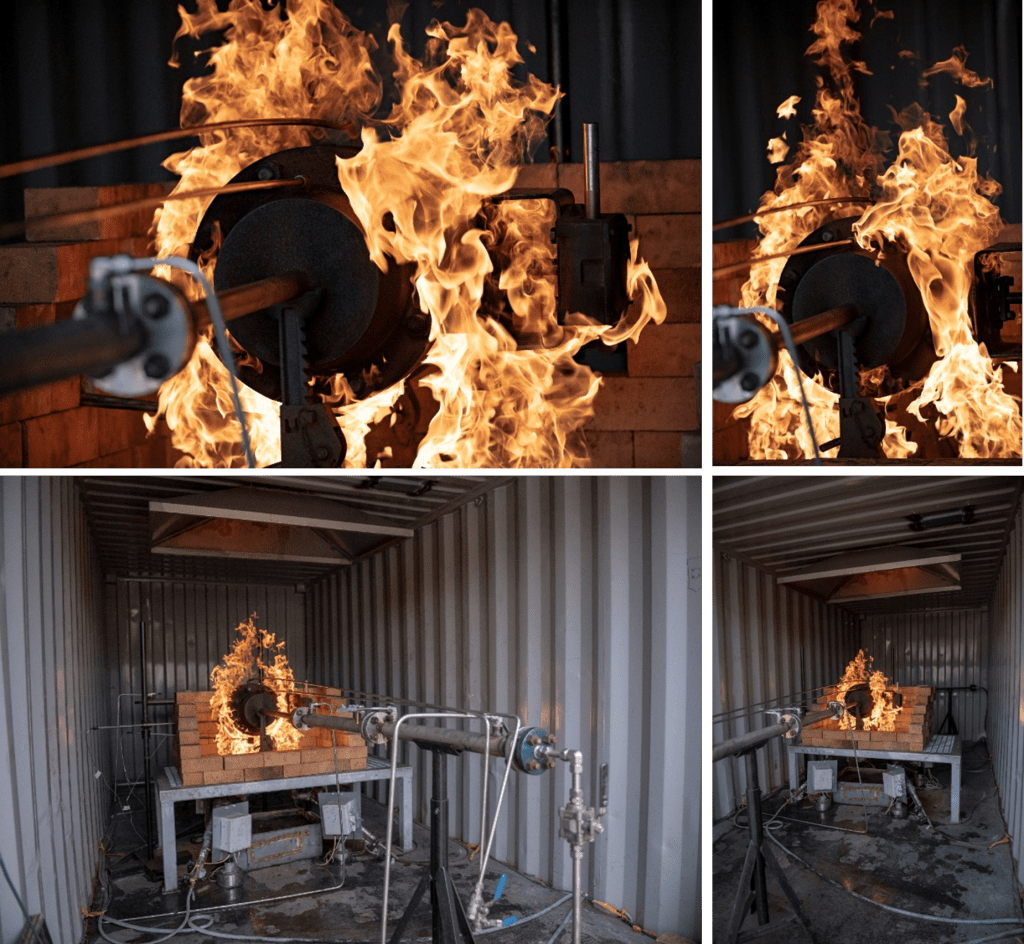
By meeting stringent fire test standards, they have provided customers with a reliable and efficient solution to fire safety. With their patented oblique cone technology, Severn have set a new benchmark for future valve designs and innovative technology and further ensure the end user achieves its core remit of safe operations and reduced downtime.
Unveiling the role of Severn’s OCT TOV Butterfly Valve in cavitation mitigation and valve protection.
Severn understands the needs and demands of critical applications and for over 60 years have been pioneering technology development to solve industry needs and provide extended service life of our products. One of the significant issues we see with severe service application valves is cavitation.
Cavitation is only evident in fluid applications and the affects are well understood. However, challenges to offer the most cost-effective solution as opposed to the correct solution, can drive users to selecting sub optimal trims for the application. Users are often expected to understand all the implications of every application(s) to ensure the best valves are selected. At Severn, our industry experts use that knowledge to ensure the best technical solution is offered every time.
Cavitation is a phenomenon that is often seen in valve applications. This can cause dangerous and costly problems to the end user as it only occurs in liquid applications and usually when the flow is being throttled. When cavitation occurs it often creates severe levels of noise and vibration that not only is hazardous to the user but can also cause considerable damage, resulting in costly and unplanned downtime and maintenance. At Severn, we have seen first-hand the effects of cavitation on trims, reducing valve lifetime from years to just weeks, through our ‘Repair Intelligence.’
Cavitation occurs when the fluid in a valve reduces in pressure to a point at which the pressure is below the vapour pressure of the fluid. But what does this mean? If we consider water boiling this is an example of the vapour pressure of a fluid being reached at atmospheric pressure. If we now put the water in a vacuum, then we can make the same fluid boil at a reduced temperature. These pressures and temperatures at which the fluid vapour pressure sits are specific to each fluid type and as such each case must be treated independently.
When a fluid passes through an orifice such as a valve or trim, we see the pressure is inversely proportional to the velocity of the fluid. As the velocity increases through the valve the pressure will decrease.
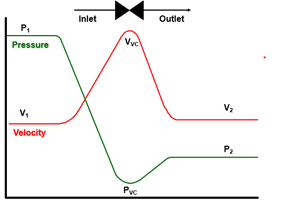
This can, in some circumstances, cause the pressure to fall below that of the vapour pressure of the fluid.
In this instance bubbles will occur in the fluid. When this happens the volume of the fluid can increase but the space inside the valve does not. This leads to the potential of increased velocity through the valve. Should there be entrained solids (such as sand) within the valve then this can have a significant erosion effect on the valve and be a cause for premature wear.
After the fluid has passed through the restriction it recovers in pressure on the other side of the orifice. This recovery in pressure and associated reduction in velocity can cause the fluid to recover above the vapour pressure of the fluid.
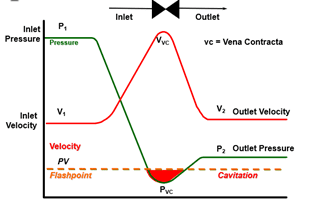
This causes the bubbles previously formed to rapidly collapse producing a shockwave. The forces involved in this are extremely violent. So much so the implosions can tear metal from components creating the characteristic pitting seen with cavitation failure.
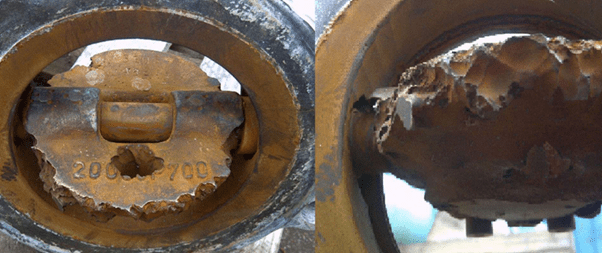
Aside from the physical damage to the valve internals, cavitation can manifest itself as loud noises, often described as “marbles in the pipeline.” These soundwaves create significant vibrations in the valves, pipework, and instrumentation, leading to failures of equipment outside of the valves flow paths due to high vibration and fatigue.
How does Severn’s OCT TOV Butterfly Valve mitigate the effects of cavitation?
By controlling the pressure drop through the valve we can prevent the onset of harmful cavitation. In a Butterfly Valve this often occurs at low openings. At these low openings we often see high velocities between the disc and valve body. Severns patented Oblique Cone Technology (OCT) allows the use of a fully circular disc and with the benefit of a true circle comes the advantage that full anti-cavitation / low noise trims can be fitted where required providing excellent cavitation control whilst still providing reliable shutoff.
In combination with the anti-cavitation disc, the OCT TOV Butterfly Valve can also be fitted with a full or half baffle as required to offer the best solution dependent on the process conditions provided.
At Severn, it is critical that the application knowledge is applied to the valve sizing to ensure the best possible solutions for the end user, ensuring costly unplanned downtime is kept to a minimum whilst achieving safe operations.
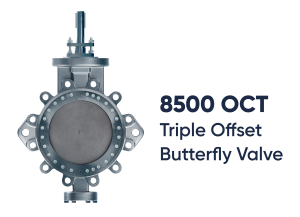
With over 60 years’ experience in the design and manufacture of Butterfly Valves, Severn launches a range built on decades of learnings and innovative engineering.
In the dynamic landscape of industrial engineering, innovation often stems from a rich heritage of expertise and an unyielding commitment to excellence. Severn Glocon, a renowned name in the world of valve design and manufacturing, have once again proven this statement true with the unveiling of the superior Oblique Cone Technology (OCT) Triple Offset (TOV) Butterfly Valve. This development represents Severn’s commitment to innovation in the realm of process and industrial energy markets, promising enhanced performance, reliability, and efficiency.
Engineering Heritage: The Foundation of Excellence
Severn’s journey to engineering eminence is woven with a tapestry of innovation and dedication stemming back over 60 years. With an engineering history extending back to 1957 and the design and manufacturing of Globe Control Valves, Severn has continuously pushed the boundaries of valve technology and design, earning a reputation for precision engineering and unmatched quality. Drawing from this extensive engineering heritage, Severn has consistently delivered solutions that exceed industry standards and address the evolving needs of diverse sectors.
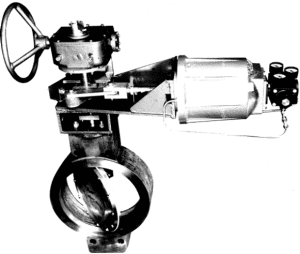
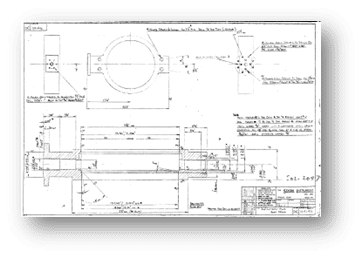
Unveiling the Oblique Cone Technology (OCT)
At the heart of Severn’s latest engineering triumph lies the OCT TOV Butterfly valve, a revolutionary advancement in Butterfly valve design and performance. Unlike traditional Butterfly valves, which often suffer from limitations in sealing performance and durability, the OCT TOV Butterfly Valve introduces circular sealing geometry.
Unlike traditional triple offset designs that use an ellipse. The benefit of circular geometry is that it provides a uniform sealing load around the circumference of the sealing diameter, providing a reliable and repeatable shut-off. By using circles rather than ellipses, it allows Severn to use proven circular sealing knowledge and incorporate this into the TOV.
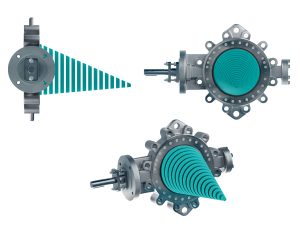
Incorporating Severn’s ‘Repair Intelligence’ knowledge which involves providing real market feedback from extensive in-depth analysis from failed valves. Severn have designed each facet of this valve to provide the most accurate, reliable, and robust service capability possible whether managing critical processes in Oil & Gas refineries, Chemical Plants, or Power Generation facilities, the OCT TOV Butterfly valve ensures the end user achieves their core remit of safe operations and minimum downtime.
Advantages for Process and Industrial Energy Markets
The introduction of the innovative OCT TOV Butterfly Valve designed by Severn signifies a paradigm shift in valve technology, offering a host of benefits to the Process & Industrial Energy markets
Enhanced Performance: Severn have designed each facet of this valve to provide the most accurate, reliable, and robust service capability possible to help the end user achieve their core remit of safe operations and minimum downtime.
Extended Lifecycle: Process conditions can change with time. Severn have ensured the interchangeability of the seal, should the sealing requirement not become as critical, or process conditions become more arduous.
Increased Safety: At Severn, safety is paramount to the design of our products and ensured that whilst adhering to the strictest industry standards, have incorporated shaft blowout prevention as a vital addition to the design of the valve to increase suitability for end users and the wider industry.
Versatility: Utilising Severn’s extended history of engineering excellence, the OCT TOV Butterfly valve has been designed for both superior control in both throttling and modulating services, whilst additionally providing a repeatable seal for isolation duties.
Environmental Sustainability: To further the commitment to reducing fugitive emissions and reduce the burden on end users to meet tightening specifications, all Severn’s OCT triple offset butterfly range offer the fugitive emissions packing sets as standard fitment on all standard valves in the range.
Severn’s relentless pursuit of engineering excellence has culminated in the development of the OCT Triple Offset Butterfly Valve – a testament to the company’s unwavering commitment to innovation and customer satisfaction. As industries worldwide seek ever-improving solutions to their operational challenges, Severn Glocon stands ready to lead the way, setting new benchmarks for performance, reliability, and efficiency in valve technology.
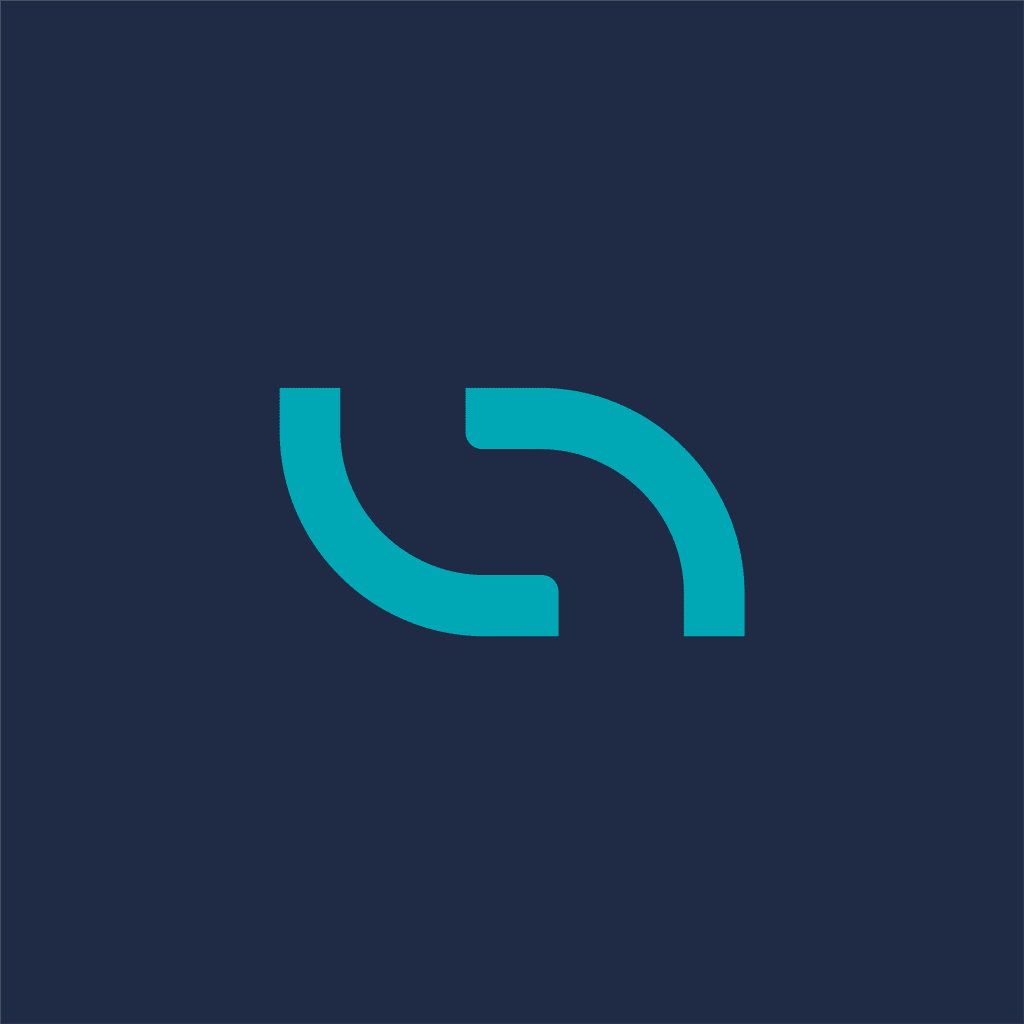
BOC praises 24-hour critical valve repair turnaround.
In the middle of February, BOC called us to investigate a recycle valve that was not stroking properly at its Worsley plant. This was a repeat problem which we’d previously resolved by adjusting the positioner. On this occasion when Field Service Technician, Jake Wood inspected the valve it was clear that the positioner needed to be replaced. Contracts Manager, Dave Morrison promptly contacted Project Engineer, Tracy Chapman in Gloucester who quickly advised us on several replacement options. One of these was already in stock in the Brighouse stores. So, Jake was despatched to BOC Worsley again the following day where he successfully installed the replacement part. This is a great example of multiple facilities collaborating to deliver a high level of customer service.
BOC praises 24-hour critical valve repair, as both the maintenance supervisor and the branch manager of BOC stated:
“I would just like to thank you for your quick response in getting our N2O filling system back up and running. This is a critical gas which we supply to the NHS and with your help and quick response we have managed to keep the supply chain going.” Mark Derbyshire, Maintenance Supervisor
“[You’ve] been a big help this week. Given the criticality of N2O, it’s prevented us having any immediate shortages to the NHS.” Dan Smith, Branch Manager
In the long-term the entire valve needs to be replaced, and Gloucester’s Tim Webb is on the case.
Severn manufactures and supports high quality valves for the energy industries. Its control, choke and small bore subsea valves are pre-eminent in the global market, underpinning the reliability and high performance of business-critical client infrastructure.
Severn’s global reach, technical prowess, and collaborative approach – all founded upon a heritage of British engineering excellence – help to assure production continuity for clients and reduce the prospect of costly downtime.
Its understanding of the life-cycle of assets positions Severn to offer end-to-end engineering solutions, enabling clients to meet their core imperatives: safe operations and minimum downtime.