Exploring the innovative features and engineering principles of Severn’s OCT TOV Butterfly Valve that puts safety first.
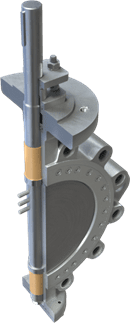
At Severn, safety is paramount in the design of our products. With our background in safety-critical industries, Severn understands the importance of safety first for both our customers and employees.
As well as adhering to the strictest industry standards, Severn have identified that shaft blowout prevention was paramount to our end users and the wider industrial and process industries for improved valve performance and reduced operational downtime.
Butterfly Valve shafts are designed to connect to the disc with either dowel pins, taper pins, or keyways. The separation of the shaft and disc in service can be catastrophically dangerous. If any of these parts fail, the shaft may be ejected from the valve body. Shaft blowouts can occur when a coupling mechanism fails, therefore, disconnecting the shaft from the disc. With the pressures in the system, it may eject the unrestrained drive shaft through either end of the valve.
Not only is this projectile a huge safety concern but has the potential to compromise the pressure envelope of the valve allowing process to escape into the atmosphere.
Severn has designed all their Triple Offset Butterfly Valves as standard with anti-blowout incorporated at both ends of the valve. This negates any chance of the shaft blowing out if the pins were to fail. The reduced shaft diameter at the drive end ensures the shaft cannot blow out through the packing follower.
On the blank end of the valve, Severn have multiple features which prevents shaft blowout. The anti-blowout ring on the threaded shaft end ensures positive engagement without the need for additional fasteners. The blank end plate is locked in place and is designed to withstand full rated test pressures.
Dual anti-blowout devices are standard on the OCT TOV Butterfly Valve, meaning that even if the gland is removed, the secondary internal anti-blowout device will stop ejection of the shaft under the pressure, thus increasing both operator and plant safety.
Severn have designed their Triple Offset Valves to exceed the minimum wall thicknesses stated in ASME B16.34. Instead of just using the minimum allowance, Severn have gone above and beyond to ensure the safety of our products in the field for our customers.
Within Severn’s Triple Offset Butterfly Valve is a corrosion allowance. This means that the valve can afford to concede material to corrosion over time without affecting the pressure containing integrity or safety of the valve. The amount of corrosion may vary depending on the environment the valve is working in, but due to Severn’s engineering heritage and excellence, the OCT TOV Butterfly Valve has been designed to withstand changes in working environments and process conditions.
High MAST figures and safety factors are key when designing the Triple Offset Butterfly Valve. MAST is the Maximum Allowable Shaft Torque a quarter turn valve shaft can withstand during operation without mechanical failure. With Severn using higher MAST figures on their Triple Offset shafts, this helps maintain the structural integrity of the valve.
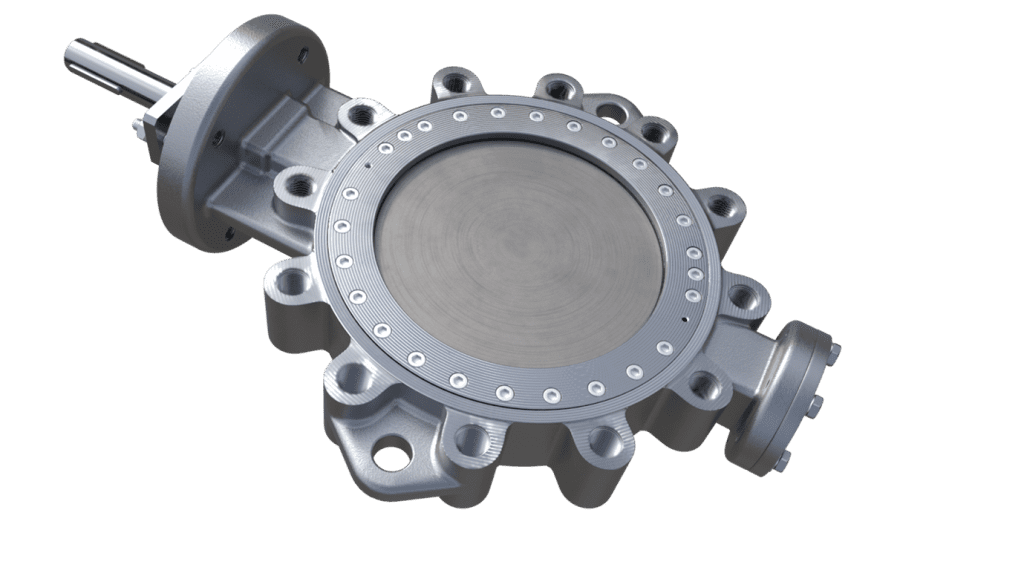
Sizing actuators correctly is a credit to Severn’s engineering excellence. Actuators, gearboxes, or any form of obturator that drives a quarter turn valve must be sized correctly by using the correct input and output torques. By torque testing the physical products prior to final inspection, we can compare the physical torques against our theoretical torques to maintain accuracy and consistency across the range.
Safety has always been at the forefront of Severn’s designs, and this is paramount in the 8500 Butterfly Valve range.
Explore the design that has been inspired by engineering heritage and excellence to create a product that master’s isolation and control applications.
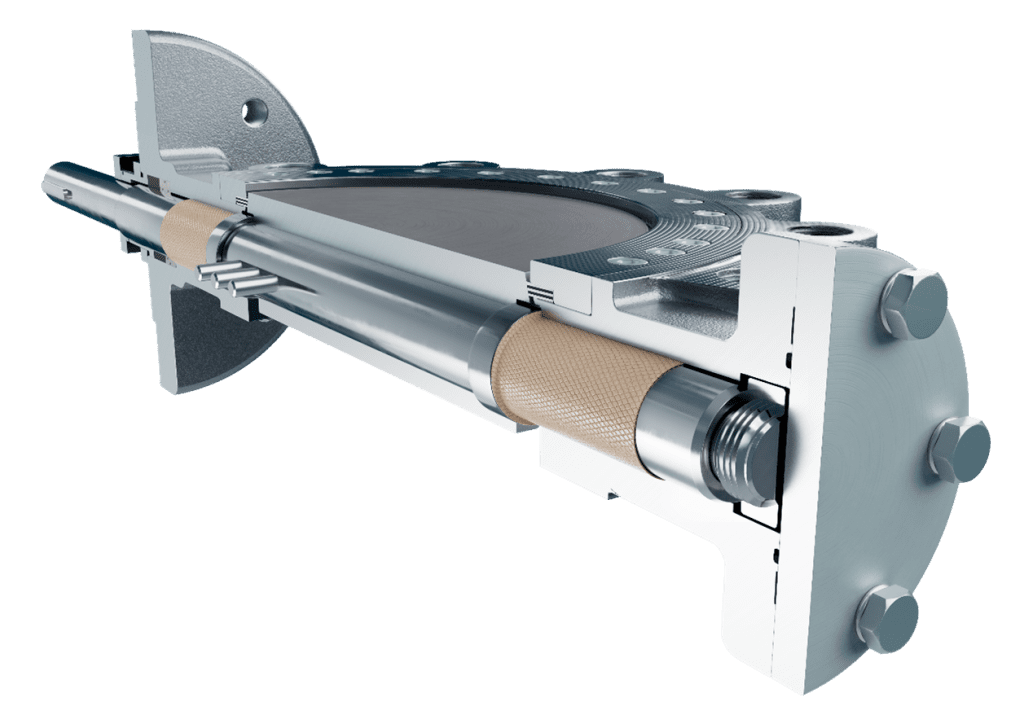
From the outset, Severn wanted the Oblique Cone Technology (OCT) to be unique in the Triple Offset valve market. Severn wanted to develop a product that not only solves an extensive range of issues for the customer with our “standard” product range, but to break tradition, and to design and manufacture a technically superior Butterfly Valve.
By utilising their comprehensive history with specialist butterfly valve design and manufacture, Severn have been able to develop a Triple Offset Butterfly Valve that performs both control and isolation duty in a single package. A valve designed from the outset to be re-used, upgraded, and provide an increased level of safety to the end user.
Severn have utilised its years of experience in manufacturing both the concentric and double offset Butterfly Valves to create innovative technology that pushes the boundaries of Triple Offset Butterfly Valve design. By looking at the traditional elliptical sealing concepts of Triple offset valves and combining this with circular sealing principals, Severn created its patented Oblique Cone Technology (OCT). In its most simplistic form, the geometry can be compared to a circular cone, by moving the point of the cone along one axis, this creates two different angles to the cone sides (forming an oblique cone), by taking a slice of this cone, it forms the sealing geometry of the OCT valve.
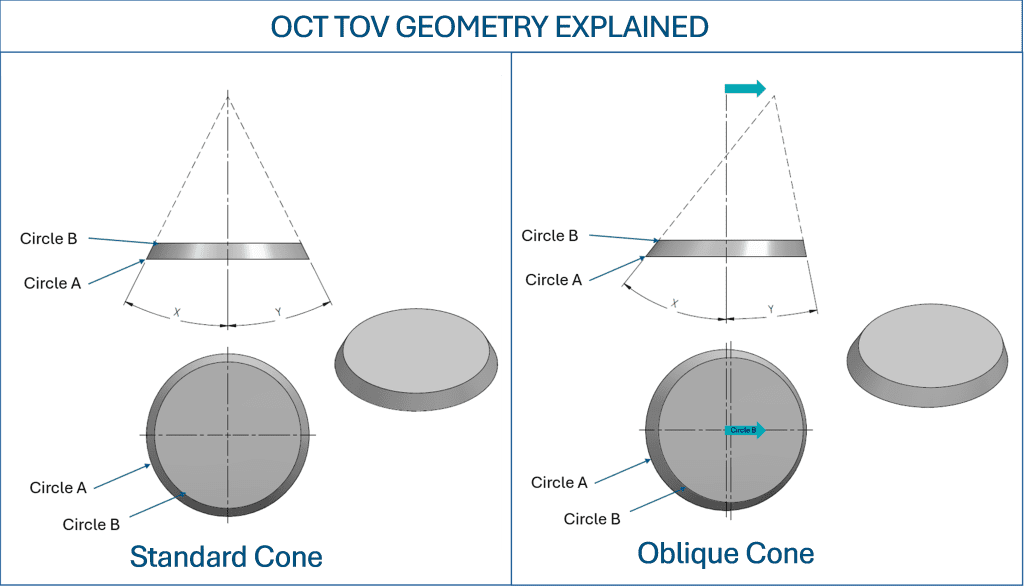
The benefit of this method means we maintain the principals of circular seals, thus providing an even seat load all-round the disc, therefore providing increased flexibility within the design to allow Severn to add different sealing options to the valve as well as specialist control trims such as anti-cavitation / low noise trims.
By understanding the foundational principals of Butterfly Valve design, Severn have a detailed knowledge of the interaction between each and every Butterfly Valve component. This combined with Severn’s Repair Intelligence philosophy and over 60 years of engineering excellence, customer solutions and end user feedback, problems can be anticipated and resolved before they occur and therefore increasing the lifecycle of the product and reducing costly unplanned downtime.
Severn additionally want to break the cycle of Butterfly Valves being a “throw away’’ commodity items. The OCT TOV Butterfly Valve is designed to be re-used, repaired, or upgraded on site with only basic tools. The robustness of the design means that the main components can be cleaned, soft goods replaced, and the valve can be reinstalled to provide extended years of reliable service. This not only reduces long term cost of ownership for the end user, but also reduces the environmental impact of the plant operations. Severn also install Fugitive Emission certified packing as standard in the OCT to further reduce the plant emission.
Flexibility and reliability come as standard in the OCT TOV Butterfly Valve. By using the principals of a Control Valve, Severn have streamlined and reduced the disc thickness to impede the flow as little as possible and maximise valve Cv. Fasteners have been removed from the disc, to eliminate the risk of them coming loose due to vibration and falling into the pipeline. The seal has also been mounted in the body rather than on the disc. This not only protects the seal by removing it from the direct flow path, but means the disc is thinner as well as giving Severn the option to add anti cavitation / low noise trims onto the disc when process conditions dictate.
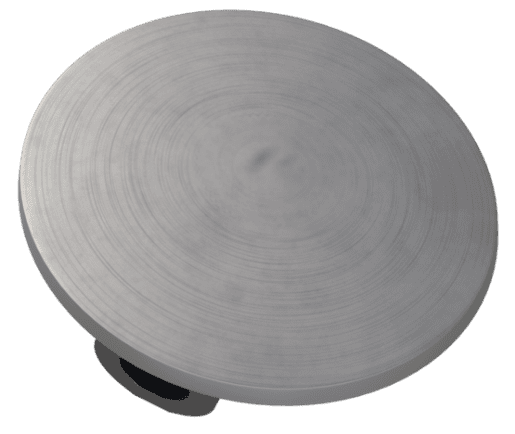
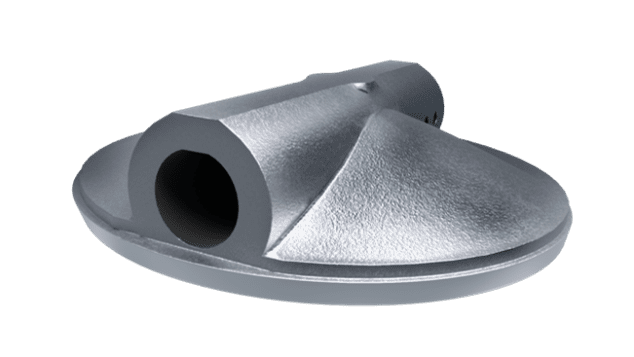
The OCT principle has been installed and operating in the field for over 10 years without issues, this coupled with countless amounts of testing and validation including fire testing, pressure testing, temperature testing and cycle testing, provide the end user with confidence in the robustness and reliability of the OCT Triple Offset Butterfly valve range and ultimately minimise down time and plant costs.

Compressor anti-surge control valves for FPSO North Sea Client delivered three days ahead of schedule
Compressor anti-surge control valves for FPSO North Sea Client delivered three days ahead of schedule
Compressor Anti-surge Control Valves delivered three days ahead of schedule
Industry : Oil & Gas FPSO
Location: UK Central North Sea
Project: Two anti-surge control valves to be delivered within a tight time frame for UK Central North Sea Client
The Challenge:
A North Sea operator needed a solution for a technically challenging anti-surge application, required on a very short delivery schedule of 16 weeks, the initial requirement was for one valve to be delivered and the second valve to be delivered 10 days later.
Finding a solution:
The Severn team made initial engagement with the client to full understand the application and performance requirements that the customer needed.
A swift coordinated approach internally by Severn’s application and engineering team was needed and the teams worked closely together as it was imperative that the issue was identified quickly so a solution could be provided, manufactured and delivered within the 16-week delivery schedule.
The product:
After identifying the clients requirements, the engineering team designed and manufactured two off 4” Cass 1500 RTJ Fig 5413 LTCS Body, SS/FC Trim, 14 Turn CCD, PC1N Pneumatic actuator with a Neles Positioner.
The positioner was revised mid order as per clients added operational requirements, the team was seamless in reacting to this change with no impact on the design or delivery schedule.
The outcome:
The contracts department managed the scope of the job and the challenges it brought professionally and with complete transparency; the client was kept fully informed throughout the production and delivery process.
The collaboration between the different departments and the constant engagement and the feedback with the client ultimately led to both valves being delivered three days in advance of the 16-week schedule, this was appreciated by the client.
The valve performed significantly well within the anti-surge required by the client for this application, especially on small step changes. This was a major issue with the clients previous valve, and an issue our team overcame with flying colours.
Severn requested to provide engineering support offshore on the asset, firstly with the installation and then subsequent valve commissioning activity.
” I want to take this opportunity to personally thank the entire Severn team for their continued focus and support during this project and more importantly, for getting both valves ready for shipping ahead of an already tight schedule.
Getting two high spec anti surge valves designed, assembled , and fully tested in less than 16 weeks is definitely an achievement” – Client representative
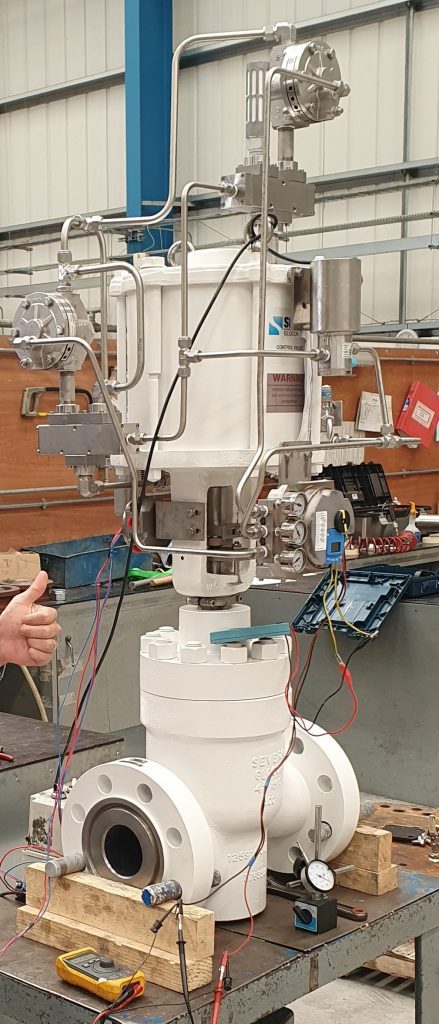
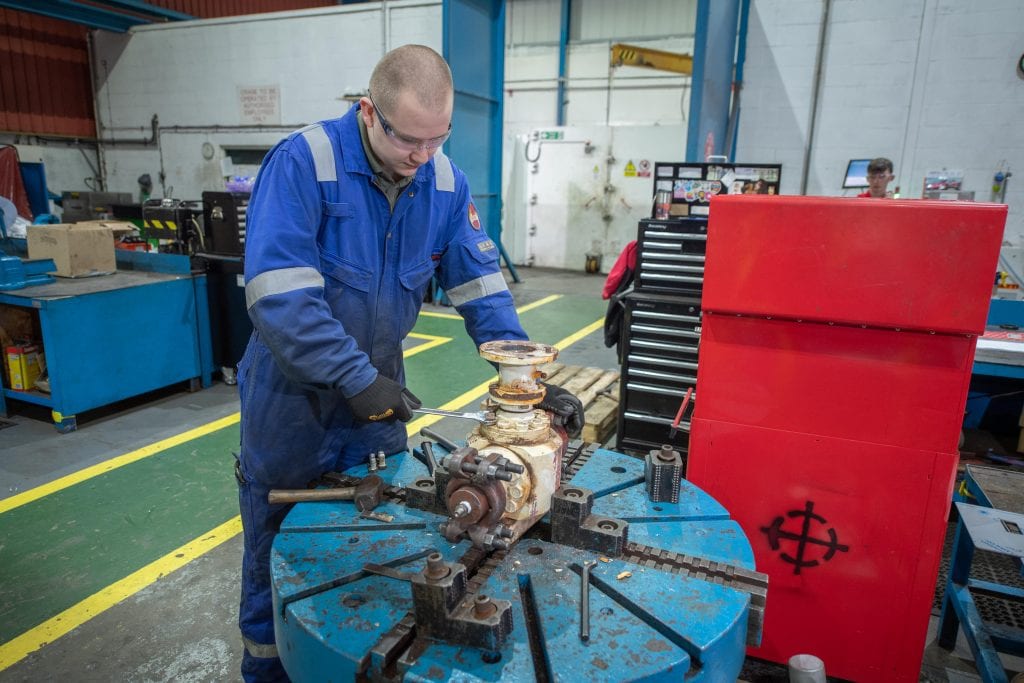
Severn Celebrates 21 years in Aberdeen.
Advanced valve engineering capabilities underpin success in the gruelling offshore oil and gas environment of the North Sea.
Enhancing the performance of existing offshore platforms has been a priority for North Sea oil and gas operators over the past two decades. With production steadily declining, finding ways to improve efficiency has been critical.
During this time, Severn has played an important role supporting leading operators with valve management and maintenance services as well as highly-engineered valve products. Longstanding client relationships are a defining feature of Severn’s business.
In 2010, Severn opened a dedicated Aberdeen facility to work in tandem with its established plant operations based then in Huddersfield and now in Brighouse. At the time, the Aberdeen team focused on the supply of traded isolation valves for North Sea operators. Today, the team works in close alignment with Brighouse under the direction of Managing Director David Brennan, as Severn’s hub for North Sea valve supply, servicing, testing and management and now Severn celebrates 21 years in Aberdeen, we are looking forward to the next years of growth and success.
Severn manufactures and supports high quality valves for the energy industries. Its control, choke and small bore subsea valves are pre-eminent in the global market, underpinning the reliability and high performance of business-critical client infrastructure.
Severn’s global reach, technical prowess, and collaborative approach – all founded upon a heritage of British engineering excellence – help to assure production continuity for clients and reduce the prospect of costly downtime.
Its understanding of the life-cycle of assets positions Severn to offer end-to-end engineering solutions, enabling clients to meet their core imperatives: safe operations and minimum downtime.
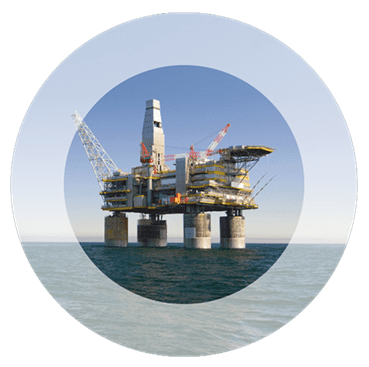
Recognition from BP.
Our Applications Engineering Group based in Brighouse received recognition from BP with a fantastic testimonial from the UK Engineering Team Leader of BP’s West Nile Delta Project this week:
“…the team in Brighouse are long overdue a thank you from us in BP West Nile Delta Operations for the support you’ve given us across various issues and various valves. We’ve bombarded you with questions and requests for data and I’m sure we’ve been a pain on more than a few occasions! However, you and the team have always responded professionally and given us very useful guidance, including going into some deep technical detail with us which has been very valuable in making our operation safer.”
Special recognition has to go to Jonny Walker and Andrew Dennis who have completed most of the work in relation to this contract.
Severn manufactures and supports high quality valves for the energy industries. Its control, choke and small bore subsea valves are pre-eminent in the global market, underpinning the reliability and high performance of business-critical client infrastructure.
Severn’s global reach, technical prowess, and collaborative approach – all founded upon a heritage of British engineering excellence – help to assure production continuity for clients and reduce the prospect of costly downtime.
Its understanding of the life-cycle of assets positions Severn to offer end-to-end engineering solutions, enabling clients to meet their core imperatives: safe operations and minimum downtime.