Severn understands the ongoing challenges operators face with reducing and eliminating fugitive emissions and have created a technical solution with the design of its Oblique Cone Technology Triple Offset Butterfly Valve.
Operators are under increasing pressure to reduce fugitive emissions for both onshore and offshore assets in order to achieve their core imperatives of safe operations and minimum downtime. Severn realises the role they play in today’s climate conscious world to help reduce and eliminate fugitive emissions from valves. Utilising the engineering heritage and extensive knowledge in severe service applications, Severn ensures it can offer the most suitable product for the end user.
Through Severn’s ‘Repair Intelligence’ and close operating relationships with end user operators, Severn has been able to understand the difficulties facing operations in the specification, purchasing and servicing of Control, Choke and Butterfly valves that are critical to reducing fugitive emissions across industrial facilities. Severn prides itself in offering technical solutions that perform no matter how severe or critical the application is. Ensuring that the end user gains the best valve performance and reduced maintenance costs over the lifecycle of the valve.
It has long been understood that approximately 60% of fugitive emissions come from valves. Even more so 80% of those emissions are related to the stem/shaft seal. Naturally, the focus is on this area with the relative fugitive emissions standards such as API 622 and ISO 15848. What is often misunderstood is the requirement for the standards to be applicable across varying temperature and pressure differentials. For this reason, Severn has 43 different certificates for sealing systems in valves based on their application requirements, up to 10,000 Psi and 425ºC. By utilising a range of materials from filled graphite through to custom PTEE-based compounds, Severn has, coupled with novel packing designs, been able to achieve tighter leakage rates that had previously been achieved with standard packing sets.
It is vital for the end user to understand the leakage class requirements when fugitive emissions are concerned to prevent over or underspecifying the solution. We often see “fugitive emissions” specified without clarification of the requirements. The various requirements from TUV through API and ISO specifications require different testing methodologies and even different testing mediums. This means that the testing standards are not directly comparable to each other. Severn often see the specification of “Low-e” or “Low emission” packing without reference to the specification. In some instances, these packing sets can have allowable leakage of up to 500ppm, many times that of systems tested to the ISO 15848-1 standard and potentially resulting in detrimental reduced on-site performance and / or higher maintenance costs.
Severn has focused and will continue to focus its testing efforts on ISO 15848 standards as it is understood that these offer the widest range of qualification options whilst not utilising harmful greenhouse gases that can be emitted using some API methodology. The fact that sealing systems are tested on the valves they are designed for and not a standard test fixture ensures maximum customer confidence in our products performance and reliability.
Severn have focused on passing some of the most stringent testing with class A leakage classes and up to 40,000 operations available for some applications. Ensuring that performance is at the heart of our product range, and you achieve your core remit of safe operations and minimum downtime.
To further the commitment to reducing fugitive emissions and reduce the burden on end users to meet tightening specifications, Severns OCT Triple Offset Butterfly Valve offers the fugitive emissions packing sets as standard fitment on all standard valves in the range. Ensuring that the end user experiences maximum valve performance in all applications.
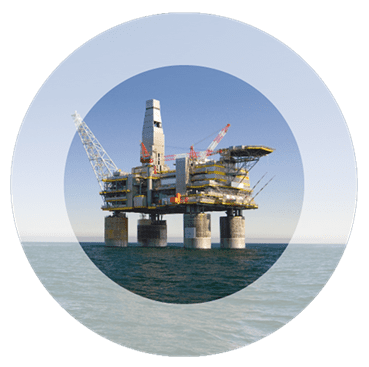
Recognition from BP.
Our Applications Engineering Group based in Brighouse received recognition from BP with a fantastic testimonial from the UK Engineering Team Leader of BP’s West Nile Delta Project this week:
“…the team in Brighouse are long overdue a thank you from us in BP West Nile Delta Operations for the support you’ve given us across various issues and various valves. We’ve bombarded you with questions and requests for data and I’m sure we’ve been a pain on more than a few occasions! However, you and the team have always responded professionally and given us very useful guidance, including going into some deep technical detail with us which has been very valuable in making our operation safer.”
Special recognition has to go to Jonny Walker and Andrew Dennis who have completed most of the work in relation to this contract.
Severn manufactures and supports high quality valves for the energy industries. Its control, choke and small bore subsea valves are pre-eminent in the global market, underpinning the reliability and high performance of business-critical client infrastructure.
Severn’s global reach, technical prowess, and collaborative approach – all founded upon a heritage of British engineering excellence – help to assure production continuity for clients and reduce the prospect of costly downtime.
Its understanding of the life-cycle of assets positions Severn to offer end-to-end engineering solutions, enabling clients to meet their core imperatives: safe operations and minimum downtime.