Discover how engineering excellence and heritage has driven Severn’s OCT TOV Butterfly Valve to deliver unmatched reliability in Seawater environments.
Severn’s research & development team has designed a Butterfly Valve that solves the problem of galvanic corrosion and meets strict fire test standards. Utilising the over 60 years of engineering excellence, the team of technical experts achieved this by using Severn’s patented Oblique Cone Technology (OCT). The OCT-SW takes this patented technology to the next level by eliminating the need for graphite in the seal and maintaining firesafe capability.
What is galvanic corrosion and its costly effects?
The impact of galvanic corrosion on critical assets due to seawater process conditions is an enduring problem for offshore oilfields. At best, it increases the workload and repairs associated with planned shutdowns. At worst it can result in rapid or unexpected damage, leading to unplanned or emergency shutdowns. Either way, it is a costly problem which harms efficiency, putting additional pressure on plant operating costs. However, Severn have utilised their engineering heritage, research and development & repair intelligence knowledge to develop a valve that deals with the issue of galvanic corrosion head on.
Why does galvanic corrosion occur? The cause of galvanic corrosion (also referred to as ‘dissimilar metal’ or ‘bimetallic’ corrosion) is an electrochemical reaction between two different conductive materials in close proximity. It results in one – the least noble of the two – being preferentially corroded. To combat this risk, the general rule is ‘do not mix metals’. However, when it comes to the design and development of assets for harsh offshore environments, things are rarely that straightforward.
Modern critical safety systems used on offshore sites are often highly sophisticated
to cope with the extreme natural conditions and industrial challenges with which they must contend. They come with extreme technical demands but must manage physical ones too; systems that need to feed water to combat fires must be durable enough to cope with the corrosive effects of the sea. Seawater service valves play an integral role in the process and their ability to either supply or isolate sections of the water line is a vital safety feature. Therefore, eliminating galvanic corrosion while maintaining firesafe credentials has been an enduring challenge for the industry.
In recent years, the use of graphite sealing technology has surged. Graphite’s extreme range of properties and characteristics makes it an ideal material in many ways. It is soft, flexible, and easy to cut, but it has high heat resistance and is almost inert. However, it is also the only non-metal that can conduct electricity. Furthermore, its nobility exceeds that of noble metals including stainless steel, bronze, and titanium. Yet it is often paired with these materials in valve manufacture, in the form of seals, packings and gaskets. From a galvanic corrosion perspective, graphite has become not only the solution to problems but can often be the cause.
Traditionally, Triple Offset Butterfly Valves have used graphite materials in their construction, which can cause galvanic corrosion in seawater applications. This is a problem because it can significantly reduce the effectiveness of the valve’s sealing components, compromising safety and leading to potential costly unplanned downtime.
By working closely with end users and operators, Severn has recognized this issue, and with its significant engineering heritage and technical expertise, has designed a long-term solution. The Severn team of engineering experts designed a valve that either replaces the graphite components completely or stops them from contacting the line media. This significantly reduces the risk of galvanic corrosion in day-to-day operations and ensures the highest level of safety. Ensuring you achieve safe operations and minimal downtime.
The Oblique Cone Technology (OCT) Seawater (SW) Triple Offset (TOV) Butterfly valve is a revolutionary type of valve designed primarily for use in saline applications, such as offshore oil and gas operations. These valves play a pivotal part in safety systems, as they play a crucial role in firewater systems. Due to Severn’s engineering heritage and technical expertise in the oil and gas operations sector, this valve has been designed with over 60 years of engineering excellence ensuring it helps the end user achieve their core remit of safe operations and minimum downtime.
Severn has developed a hybrid polymer metallic seal that moves away from the use of graphite laminates. By utilising a primary metallic seal with a secondary polymer seal, not only have Seven removed the graphite from the seal but have additionally increased the valves isolation sealing capabilities and maintained the firesafe performance crucial for such critical applications. This coupled with isolating any graphite gaskets and packings from encountering the line media means that at no point during the normal operation of the valve do the graphite and seawater mix, eliminating the risk of galvanic corrosion and the costly effects it can have on production.
In addition to addressing the corrosion problem, Severn’s Butterfly Valves also meet important fire test standards such as API 6FA, API 607, and ISO 10497 accreditations. As such the OCT Valve is certified fire-safe and can be relied upon in critical emergencies for the end user and operators, ensuring safe operations and minimal downtime.
The team also took steps to ensure the valve design could not generate a spark and risk starting a fire itself. They followed the ISO/IEC 80079-36:2018 ATEX standard and ensured that no static charge could build within the valve. This additional element of care renders the new OCT-SW valve design suitable for a wide range of applications, beyond seawater service further emphasising the versatility of the valve design.
The OCT-SW can be manufactured from corrosion-resistant materials such as Aluminium Bronze, Super Duplex, and Titanium, with the added knowledge that anti-blowout protection comes as standard. Available in standard and non-standard face to face dimensions and various body styles such as lugged and double flanged, the valve can be easily retrofitted into existing pipeline spaces and is an ideal upgrade when operators are experiencing issues with galvanic corrosion.
Severn’s engineering heritage and technical expertise have led to the OCT TOV Butterfly Valve being future-proof for changes in the process conditions to provide increased versatility for the end user.
From the outset, Severn made flexibility a key driving force in the design of the Oblique Cone Technology (OCT) Triple Offset (TOV) Butterfly Valve. Due to Severns extensive diverse engineering heritage and excellence, our expert team of engineers understand that processes and application product demands change over time, whether it is the process conditions or the overall requirements of the valve for the end user. Due to this understanding, the Oblique Cone Technology Triple Offset Butterfly Valve has been designed to incorporate multiple seal options, all fully interchangeable with each other, providing maximum application diversity and usability to ensure safe operations and minimum downtime.
The Laminate seal is the “traditional” Triple Offset Valve seal and consists of multiple metal and graphite layers providing isolation sealing.
The OCT HS seal is a hybrid polymer metallic seal, this seal benefits from a primary metal seal and secondary polymer seal, this provides a reliable and repeatable bubble tight seal time after time. This can also be paired with PTFE packings when graphite being in contact with the line media is a concern. The polymer seal is fully compliant with EN ISO 80079-36 (ATEX).
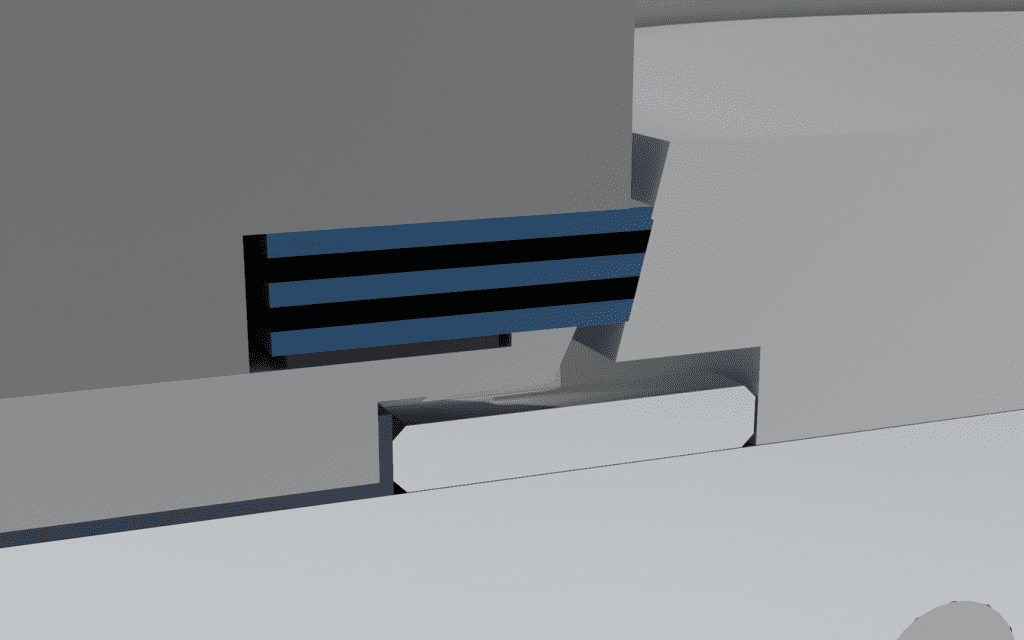
The OCT SW Valve takes the hybrid sealing to the next level with its versatile high performance. Severn utilises the OCT-HS seal and has designed a valve that ensure there is no graphite in contact with the line media to remove the risk of costly galvanic effects such as internal corrosion leading to valve failure. Whilst doing so the OCT-SW also maintains firesafe certification.
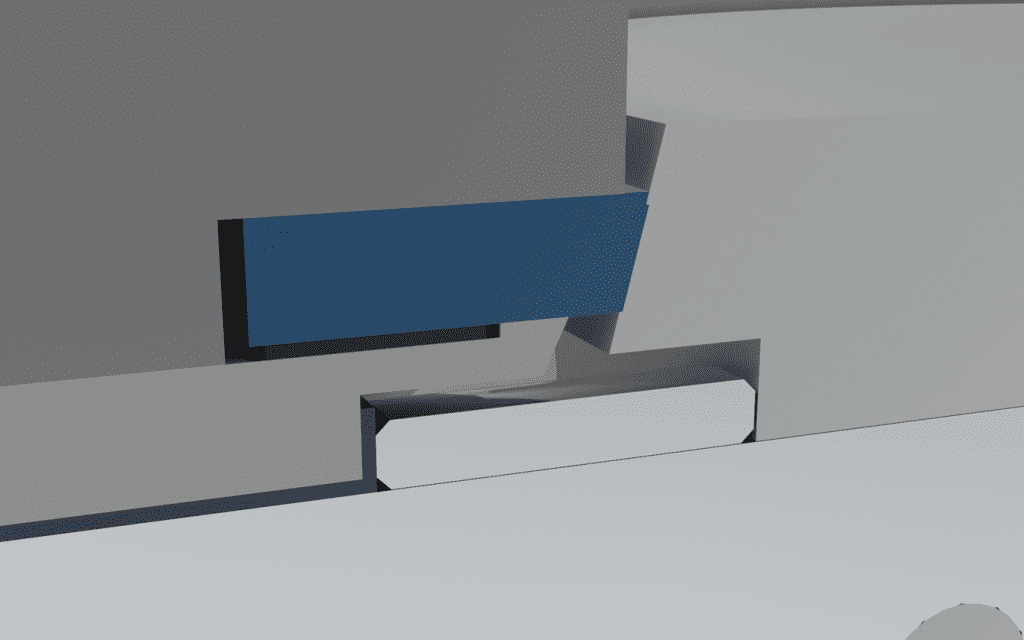
Should the sealing requirement not become as critical, and process conditions become more arduous, the Laminate and Hybrid seals can be changed for the OCT-SS solid seal. As the name suggests it is a solid metallic seal, that can be made from hard-wearing alloys to add longevity to the sealing life of the valve in arduous conditions and can offer a control valve seat leakage.
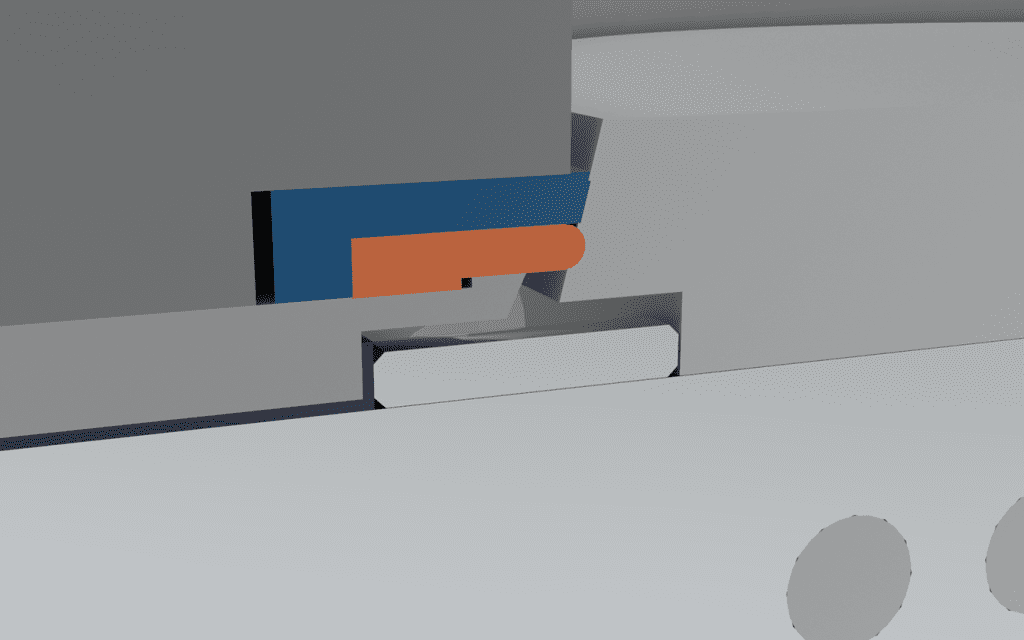
Based on Severns comprehensive history of severe service control, our team of engineering experts work closely with operators and end uses to identify the correct seal and material selection to provide the maximum reliability and productivity further ensuring minimum downtime.
All the OCT seals are interchangeable and can be upgraded without the need for main valve components being replaced, further emphasising the OCT TOV Butterfly Valves versatility. The fully in field serviceable valve can be upgraded on-site without the need for specialist tools or knowledge, this further ensures that costly unplanned downtime and site waste is kept to a minimum, along with potential loss in production for the end user. All the seal options can be changed on site within a small space of time to ensure site maintenance costs are reduced by upgrading the existing valve rather than discarding and replacing with a commodity product each time.
Each OCT valve is specially designed to be versatile and ensure it has multiple purposes for multiple conditions whilst still delivering maximum performance. With the introduction of the interchangeable seal, these can be easily swapped out to match the end users’ requirements, should they change.
The Triple Offset Butterfly Valve Cutting Edge Design Features Leads to Comprehensive Application Coverage.
Incorporating over 60 years of engineering excellence and technical expertise in valve engineering and application, Severn offers an industry leading and patented engineering technology solution(s) for Butterfly Valve requirements and applications with the Oblique Cone Technology (OCT) Triple Offset (TOV) Butterfly Valve. By utilising Severn’s ‘Repair Intelligence’ knowledge which involves providing real market feedback from extensive in-depth analysis from failed valves. Severn have designed each facet of the OCT TOV Butterfly Valve to provide the most accurate, reliable, and robust service capability and performance possible to help the end user achieve their core remit of safe operations and minimum downtime.
Severn’s OCT design uses circular sealing geometry, unlike traditional triple offset designs that use an ellipse. The benefit of circular geometry is that it provides a uniform sealing load around the circumference of the sealing diameter, providing a reliable and repeatable shut-off. By using circles rather than ellipses, it allows Severn to use proven circular sealing knowledge and incorporate this into the TOV Butterfly Valve.
In addition, to this we can also add specialised flow control trims that are traditionally found on double offset valves. These control trims include Anti Cavitation / Low noise, half baffle & full baffles. We can also add special features such as steam jacket and purge ports should they be required, onto our Triple Offset design.
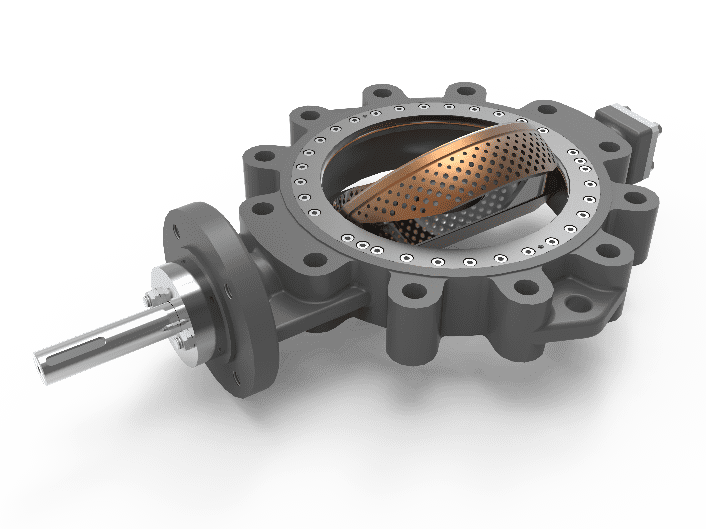
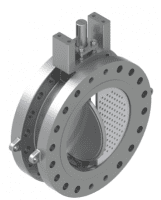

Process conditions can change with time. Severn have ensured the interchangeability of the seal, should the sealing requirement not become as critical, or process conditions become more arduous. The HS seal can be changed to a laminated seal, or if conditions dictate, a solid seal. This can be done without the need for main valve components being replaced. The complete in-field serviceable valve can be upgraded on site without the need for specialist tools or knowledge ensuring possible down time and loss in production is kept to a minimum.
The interchangeability and versatility of the seal allows for Severn’s Triple Offset Valve to be used for both isolation and control applications and processes. The diversity of the OCT TOV Butterfly Valve and its functional usability for an extensive range of both isolation and control applications leads to the potential savings in stock holdings for end users who can use stock this one valve instead of stocking two. This in turn allows for potential cost savings for the end user on stock holding by reducing the need to stock multiple valves due to the extensive coverage that the OCT TOV Butterfly Valve offers.
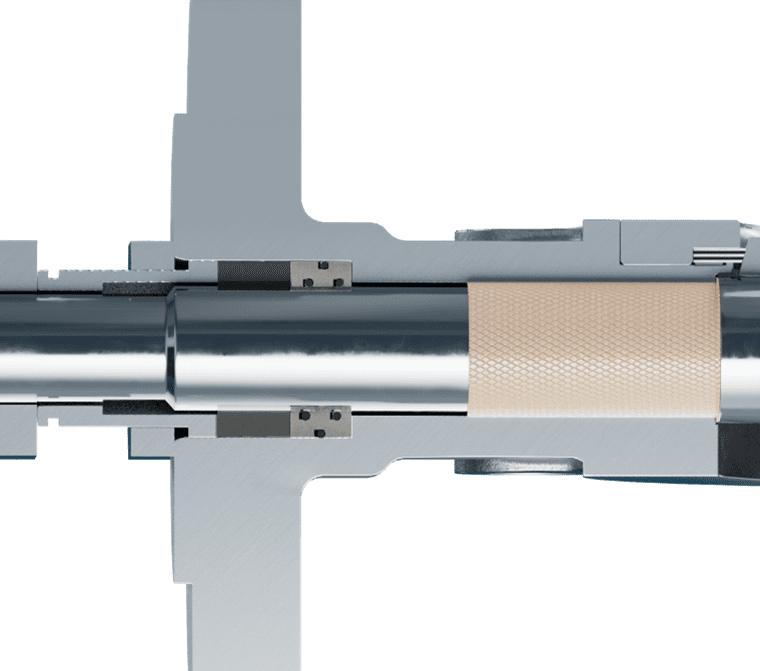
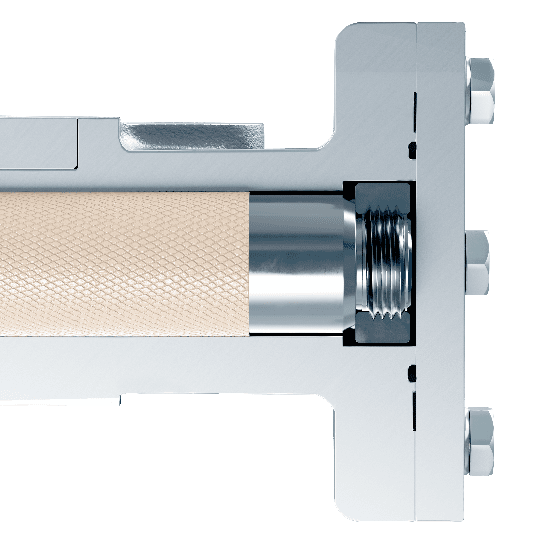
Severn have designed all their Triple Offset Butterfly Valves with safety as paramount and therefore engineered the product with anti-blowout at both ends of the valve. This negates any chance of the shaft blowing out. The reduced shaft diameter at the drive end ensures the shaft cannot blow out through the packing follower and anti-blowout ring on the threaded shaft end ensures positive engagement without the need for additional fasteners.
The OCT range also comes with hard facing on the disc as standard with options to upgrade the standard hard facing to weld overlays such as stellite 6, ensuring and reliable seal and extended service life.
A quarter turn design ensures ease of actuation for both control and isolation purposes. Whether this be via an actuator or gearbox, the quarter turn design allows for simple operation.
As standard, Severn’s OCT TOV Butterfly Valve includes fugitive emission packing to ISO 15848 with options to change to meet customer specific requirements such as Shell 77/312 available.
The OCT valve range has been firesafe tested & certified in accordance with the strict fire test specifications set out in the standards ISO 10497, API 607 & API 6FA. Withstanding extreme temperatures of up to 1000°C whilst still sealing. Further underpinning the performance capabilities and validating the valve performance, ensuring this valve can be suitable for an extended range of applications and process requirements, leading to safe operations and reduction unplanned downtime for the end user.
Severn offer the OCT TOV Butterfly Valve in all cast materials. From basic carbon steels to specialist alloys such as Monel, Titanium & Hastelloy. Severn can provide the correct material selection for your application. Additional surface coatings such as stellite, armoloy, chrome or weld overlays are available upon application and request.
Severn are breaking tradition with the innovative OCT Butterfly Valve and lifecycle enhancement service.
In the fast-paced industrial landscape, the emphasis on sustainability and cost-effectiveness has never been greater. Severn’s Oblique Cone Technology (OCT) Triple Offset (TOV) Butterfly Valve is at the forefront of a new era in valve technology, where the focus shifts from immediate replacements to intelligent lifecycle enhancement and repair strategies. This paradigm shift not only promotes sustainable valve maintenance but also ensures safe operations, reduced downtime, helping you achieve your core remits.
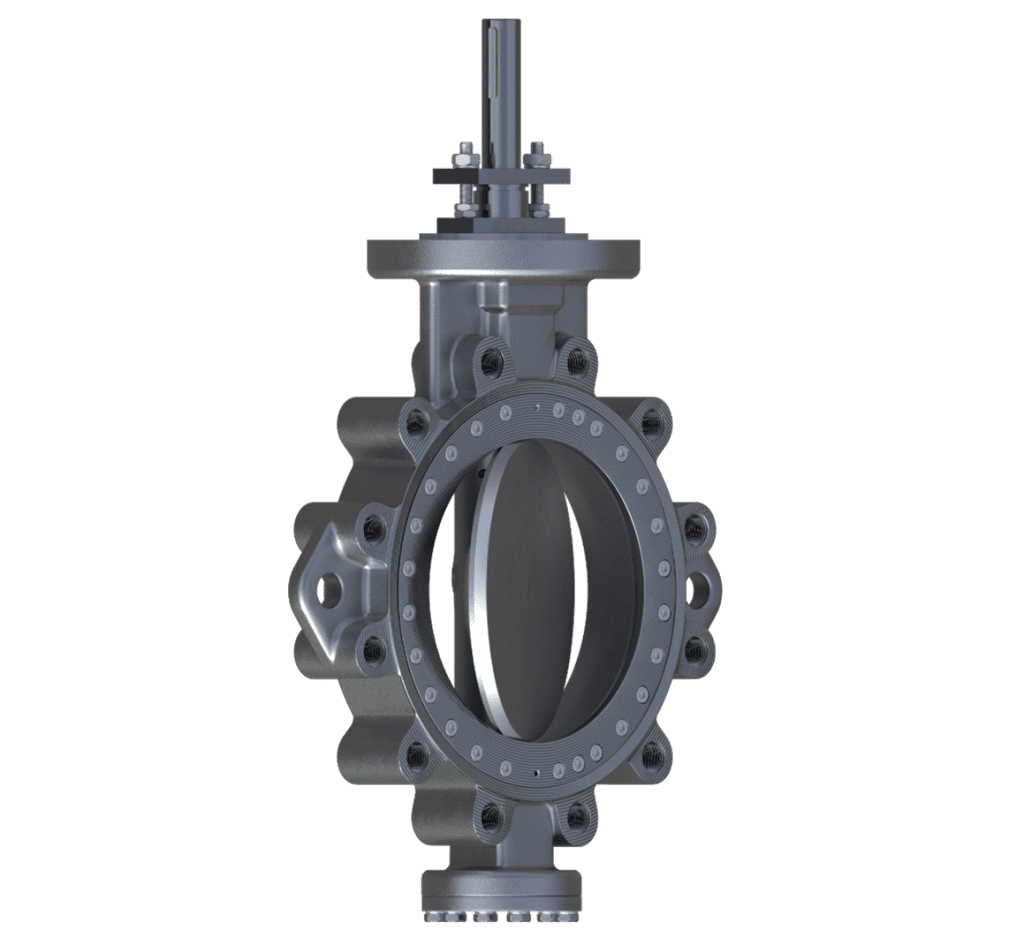
Lifecycle Enhancement: Prolonging Valve Longevity
The traditional approach to valve maintenance often involves a “replace-first” mentality. However, Severn’s OCT TOV Butterfly Valve challenges this norm by offering a comprehensive lifecycle enhancement program. Through cutting-edge innovative engineering and materials, the OCT TOV Butterfly Valve is designed to withstand harsh operating conditions, ensuring a longer lifespan with its patented Oblique Cone Technology Triple Offset capabilities for both isolation and control applications.
By prioritizing lifecycle enhancement, industries can optimise their assets, reduce overall operational costs, and minimise the environmental footprint associated with the manufacturing and disposal of new valves.
Repair Intelligence: Smart Solutions for Complex Issues
The OCT TOV Butterfly Valve affirms the concept of Severn’s repair intelligence as the valves are designed with modular components, facilitating easy disassembly and reassembly during repairs. This not only reduces maintenance costs but also minimises the need for complete valve replacements, contributing to a more sustainable and cost-effective approach to industrial operations.
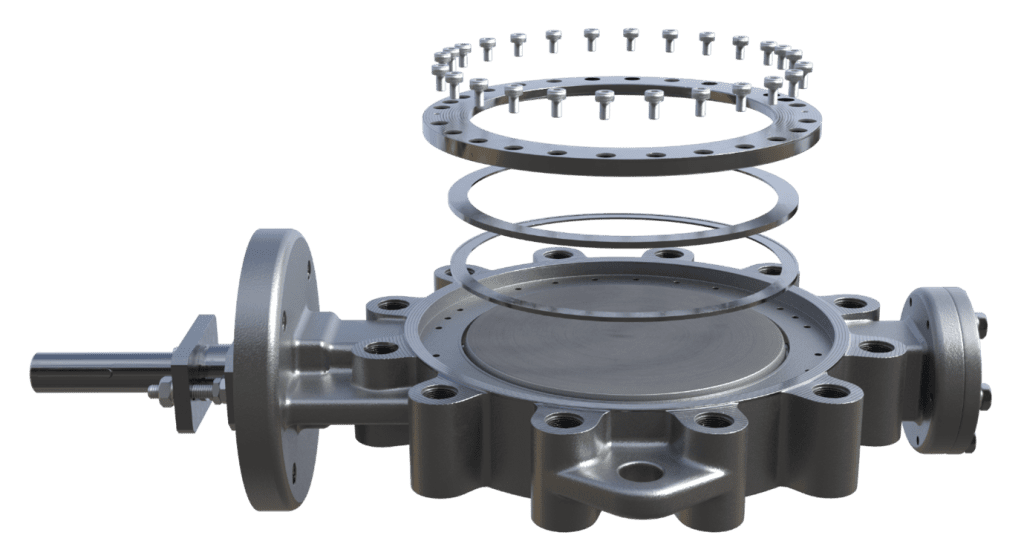
Sustainable Valve Maintenance: A Green Approach
Severn’s commitment to sustainability goes beyond the valve’s design. The OCT TOV Butterfly Valve promotes a circular economy by encouraging refurbishment and reconditioning of components. With our expert team of service engineers based globally, we can retrofit, service and repair any of our Butterfly valves on site if performance has dropped or specification or operating conditions have changed, this ensures production downtime is kept to a minimum.
Furthermore, sustainable valve maintenance aligns with global initiatives to reduce carbon emissions. By extending the life of industrial equipment, companies can decrease their carbon footprint associated with manufacturing and disposal, contributing to a greener and more environmentally responsible future.
Safe Operations and Reduced Downtime: The Ultimate Value Proposition
The OCT TOV Butterfly Valve prioritise safety through rigorous testing and compliance with industry standards such as API 598. By implementing repair intelligence and lifecycle enhancement strategies, Severn can ensure the continued reliability and safety of their valves and valve systems.
Moreover, the ability to address issues proactively minimise unexpected costly downtime. This not only enhances operational efficiency but also safeguards against potential safety hazards, ensuring a secure working environment for personnel.
Environmental Impact: A Positive Footprint for Future Generations
By choosing repair over replacement and embracing Severn’s lifecycle enhancement, industries using Severn’s OCT TOV Butterfly Valve actively contribute to reducing the environmental impact of their operations. Through sustainable valve maintenance practices, companies can align with global environmental goals, demonstrating corporate responsibility and leadership in their respective sectors.
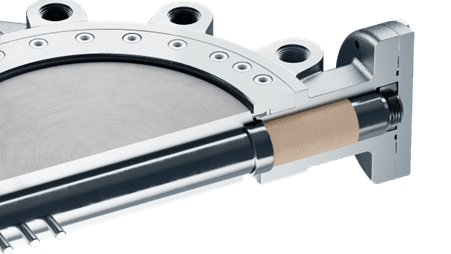
Severn’s OCT TOV Butterfly Valve signifies a paradigm shift in the industrial valve landscape. By championing lifecycle enhancement, repair intelligence, and sustainable valve maintenance, this product offers not just cutting-edge technology but a comprehensive solution for industries seeking a balance between operational efficiency, environmental responsibility, and cost-effectiveness. In a world where every decision impacts the planet, choosing to repair, not replace, is a step towards a more sustainable and resilient future.
Unveiling the role of Severn’s OCT TOV Butterfly Valve in cavitation mitigation and valve protection.
Severn understands the needs and demands of critical applications and for over 60 years have been pioneering technology development to solve industry needs and provide extended service life of our products. One of the significant issues we see with severe service application valves is cavitation.
Cavitation is only evident in fluid applications and the affects are well understood. However, challenges to offer the most cost-effective solution as opposed to the correct solution, can drive users to selecting sub optimal trims for the application. Users are often expected to understand all the implications of every application(s) to ensure the best valves are selected. At Severn, our industry experts use that knowledge to ensure the best technical solution is offered every time.
Cavitation is a phenomenon that is often seen in valve applications. This can cause dangerous and costly problems to the end user as it only occurs in liquid applications and usually when the flow is being throttled. When cavitation occurs it often creates severe levels of noise and vibration that not only is hazardous to the user but can also cause considerable damage, resulting in costly and unplanned downtime and maintenance. At Severn, we have seen first-hand the effects of cavitation on trims, reducing valve lifetime from years to just weeks, through our ‘Repair Intelligence.’
Cavitation occurs when the fluid in a valve reduces in pressure to a point at which the pressure is below the vapour pressure of the fluid. But what does this mean? If we consider water boiling this is an example of the vapour pressure of a fluid being reached at atmospheric pressure. If we now put the water in a vacuum, then we can make the same fluid boil at a reduced temperature. These pressures and temperatures at which the fluid vapour pressure sits are specific to each fluid type and as such each case must be treated independently.
When a fluid passes through an orifice such as a valve or trim, we see the pressure is inversely proportional to the velocity of the fluid. As the velocity increases through the valve the pressure will decrease.
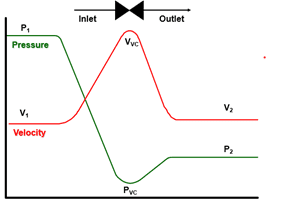
This can, in some circumstances, cause the pressure to fall below that of the vapour pressure of the fluid.
In this instance bubbles will occur in the fluid. When this happens the volume of the fluid can increase but the space inside the valve does not. This leads to the potential of increased velocity through the valve. Should there be entrained solids (such as sand) within the valve then this can have a significant erosion effect on the valve and be a cause for premature wear.
After the fluid has passed through the restriction it recovers in pressure on the other side of the orifice. This recovery in pressure and associated reduction in velocity can cause the fluid to recover above the vapour pressure of the fluid.
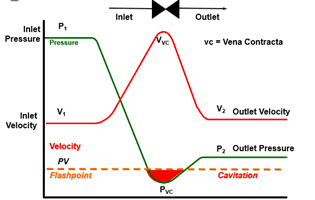
This causes the bubbles previously formed to rapidly collapse producing a shockwave. The forces involved in this are extremely violent. So much so the implosions can tear metal from components creating the characteristic pitting seen with cavitation failure.
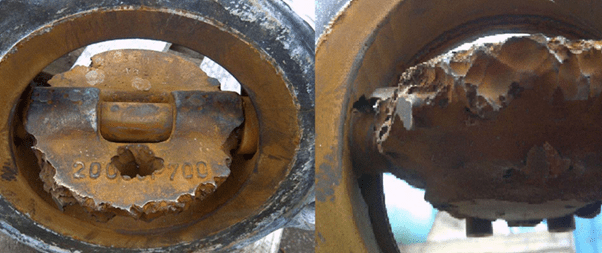
Aside from the physical damage to the valve internals, cavitation can manifest itself as loud noises, often described as “marbles in the pipeline.” These soundwaves create significant vibrations in the valves, pipework, and instrumentation, leading to failures of equipment outside of the valves flow paths due to high vibration and fatigue.
How does Severn’s OCT TOV Butterfly Valve mitigate the effects of cavitation?
By controlling the pressure drop through the valve we can prevent the onset of harmful cavitation. In a Butterfly Valve this often occurs at low openings. At these low openings we often see high velocities between the disc and valve body. Severns patented Oblique Cone Technology (OCT) allows the use of a fully circular disc and with the benefit of a true circle comes the advantage that full anti-cavitation / low noise trims can be fitted where required providing excellent cavitation control whilst still providing reliable shutoff.
In combination with the anti-cavitation disc, the OCT TOV Butterfly Valve can also be fitted with a full or half baffle as required to offer the best solution dependent on the process conditions provided.
At Severn, it is critical that the application knowledge is applied to the valve sizing to ensure the best possible solutions for the end user, ensuring costly unplanned downtime is kept to a minimum whilst achieving safe operations.
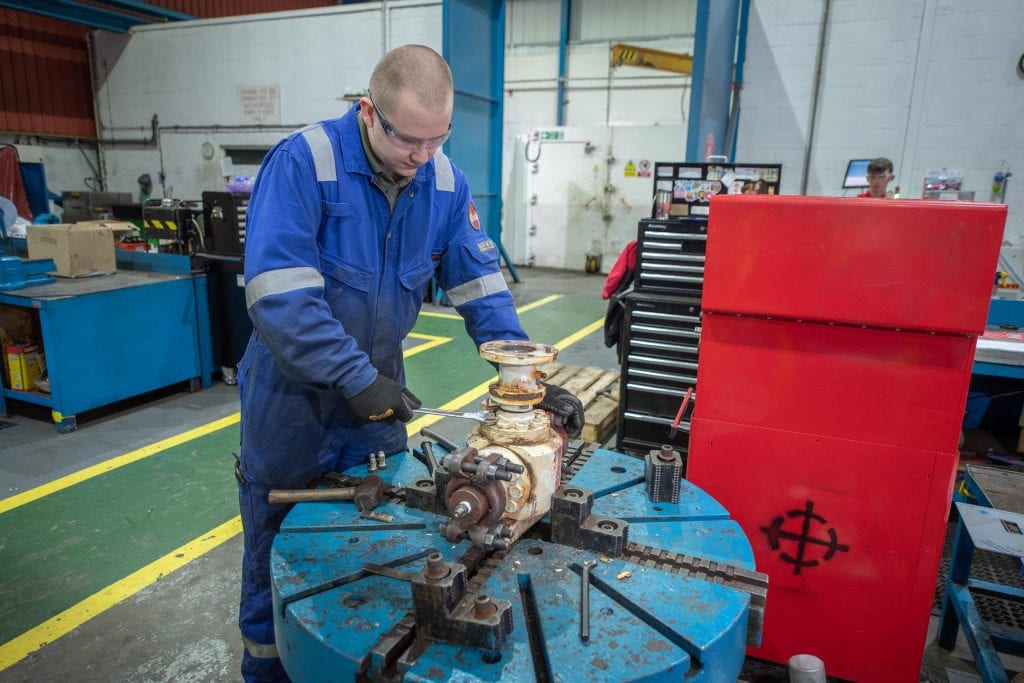
Severn Celebrates 21 years in Aberdeen.
Advanced valve engineering capabilities underpin success in the gruelling offshore oil and gas environment of the North Sea.
Enhancing the performance of existing offshore platforms has been a priority for North Sea oil and gas operators over the past two decades. With production steadily declining, finding ways to improve efficiency has been critical.
During this time, Severn has played an important role supporting leading operators with valve management and maintenance services as well as highly-engineered valve products. Longstanding client relationships are a defining feature of Severn’s business.
In 2010, Severn opened a dedicated Aberdeen facility to work in tandem with its established plant operations based then in Huddersfield and now in Brighouse. At the time, the Aberdeen team focused on the supply of traded isolation valves for North Sea operators. Today, the team works in close alignment with Brighouse under the direction of Managing Director David Brennan, as Severn’s hub for North Sea valve supply, servicing, testing and management and now Severn celebrates 21 years in Aberdeen, we are looking forward to the next years of growth and success.
Severn manufactures and supports high quality valves for the energy industries. Its control, choke and small bore subsea valves are pre-eminent in the global market, underpinning the reliability and high performance of business-critical client infrastructure.
Severn’s global reach, technical prowess, and collaborative approach – all founded upon a heritage of British engineering excellence – help to assure production continuity for clients and reduce the prospect of costly downtime.
Its understanding of the life-cycle of assets positions Severn to offer end-to-end engineering solutions, enabling clients to meet their core imperatives: safe operations and minimum downtime.
United Kingdom, 23rd June 2021: Severn Glocon UK Valves Limited and ValvTechnologies have reached an agreement to form a strategic partnership that will see collaboration between two of the world’s leading engineering and manufacturing companies specializing in innovative, high-end, severe-service valves.
Subject to regulatory approval in the U.S., Severn and ValvTechnologies strategic partnership will combine the brands’ distinctive and complementary capabilities to extend the global reach, product offerings and customer service of both companies. Backed by Bluewater, the international energy private equity firm, the collaboration will see many customer and sales synergies that will offer significant added value to the marketplace.
Headquartered in the UK and with premises worldwide, notably manufacturing facilities in India, Severn specializes in control, choke and small-bore subsea valves for the energy industry. Headquartered in Houston, Texas, ValvTechnologies also has premises worldwide, and is the global leader in the design and manufacture of metal-seated, zero-leakage, severe-service valve solutions for the harshest applications.
Kevin Hunt, President at ValvTechnologies, comments: “Both Severn and ValvTechnologies have a long history of mutual respect. Now, working more closely together, we can provide a broader range of engineered solutions to the severe-service marketplace. That’s great news for our customers.”
Steve Waugh, Chairman of Severn, adds: “Each company has been founded on technical prowess and commitment to innovation. Through this new combined force for the global valve market, we believe we will provide an enviable range of solutions and services in our industries.”
About Severn
Founded in 1961 and headquartered in Gloucester, United Kingdom, Severn Glocon UK Valves Limited is a leading manufacturer of control valves and related products worldwide. The company offers a wide range of severe service control, choke and general service valves, associated actuators and peripheral equipment, bespoke built special application control & choke valves, providing valve management as well as general engineering support services to oil and gas, LNG, power and other process plant users.
About ValvTechnologies
Founded in 1987 and headquartered in Houston, Texas, ValvTechnologies is the leading manufacturer of zero-leakage, high-performance isolation valve solutions providing an unsurpassed level of severe service isolation services and reliability to customers in the fossil power, nuclear generation, upstream oil and gas, downstream and chemical processing, mining and minerals, pulp and paper and other specialized industries.
About Bluewater Bluewater is a specialist international private equity firm focused on the middle-market energy sector. Its experienced investment and operating professionals drive value creation as they manage $2.5billion of investment across a portfolio of 22 companies. Today it has a prime focus on projects or technologies that contribute to the energy transition agenda, and works to a diversified investment strategy based on the principles of sustainability and close working partnerships with best-in-class management teams. It has a strong focus on ESG, and is a signatory to the UN Principles for Responsible Investment.
Media contacts
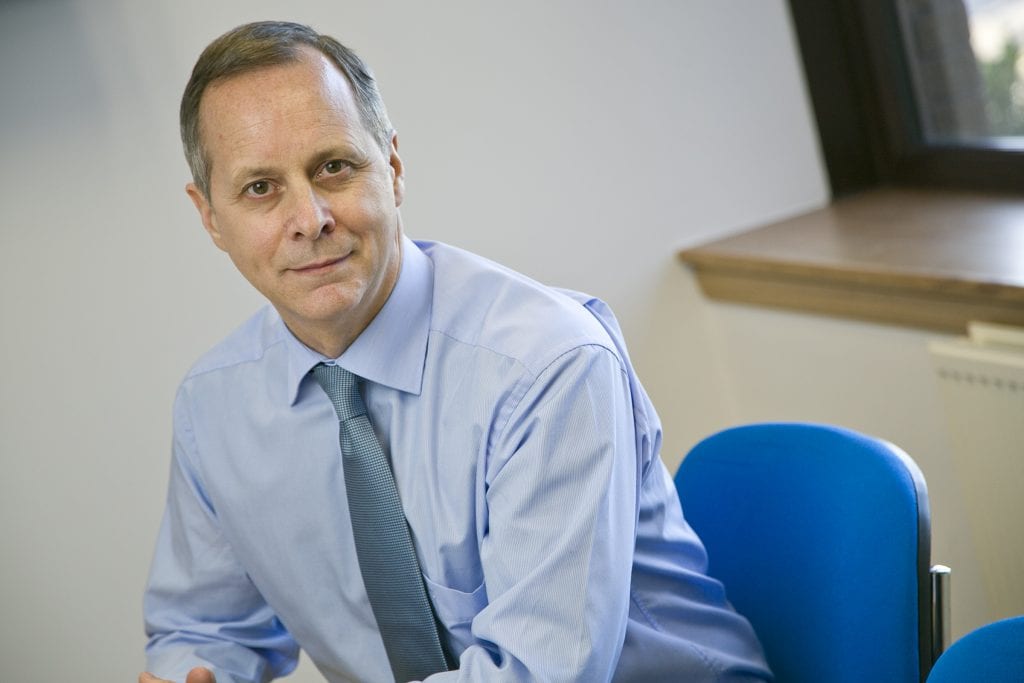
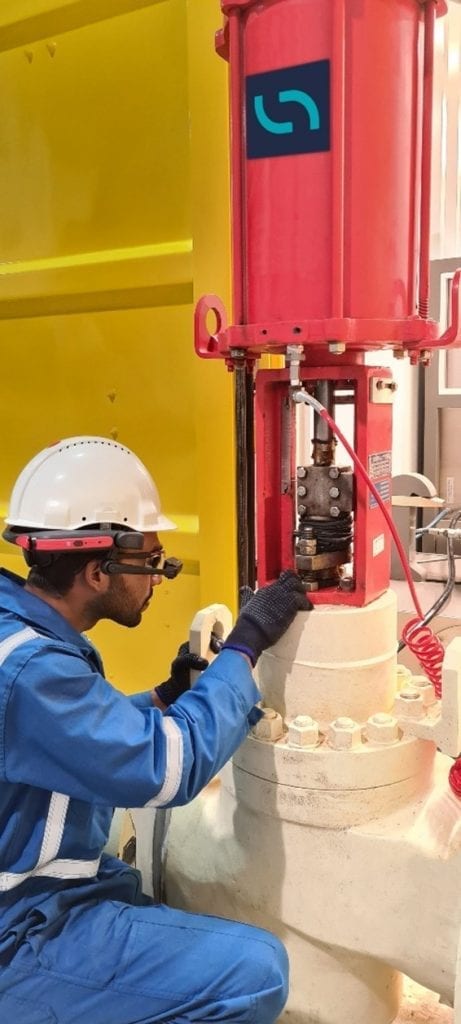
Remote inspection technology gains momentum.
Adoption of Severn Oculi, our connected system for the remote inspection of valves, is going from strength to strength. As well as assessing valve condition in the field, the digital system can be used to facilitate remote witness testing.
Severn Glocon Abu Dhabi recently conducted a full pressure, seat leakage and functional test on a 2- 9/16 API 10,000 globe control valve for ADNOC, with the process witnessed virtually by the client team. Various work scopes have been witness-tested in this way in recent weeks to demonstrate the technology to our clients.
The SVS team has also been holding internal video conferences to introduce the technology and its benefits to the wider Group. If you would like to participate in a future demonstration, please contact support@svsi.ae.
With the global pandemic response still restricting movements and international travel, remote inspection technology gains momentum as Severn Oculi is proving to be a valuable tool. It’s set to deliver a good return on investment, improving cost efficiency for Severn and our customers alike.
Severn manufactures and supports high quality valves for the energy industries. Its control, choke and small bore subsea valves are pre-eminent in the global market, underpinning the reliability and high performance of business-critical client infrastructure.
Severn’s global reach, technical prowess, and collaborative approach – all founded upon a heritage of British engineering excellence – help to assure production continuity for clients and reduce the prospect of costly downtime.
Its understanding of the life-cycle of assets positions Severn to offer end-to-end engineering solutions, enabling clients to meet their core imperatives: safe operations and minimum downtime.
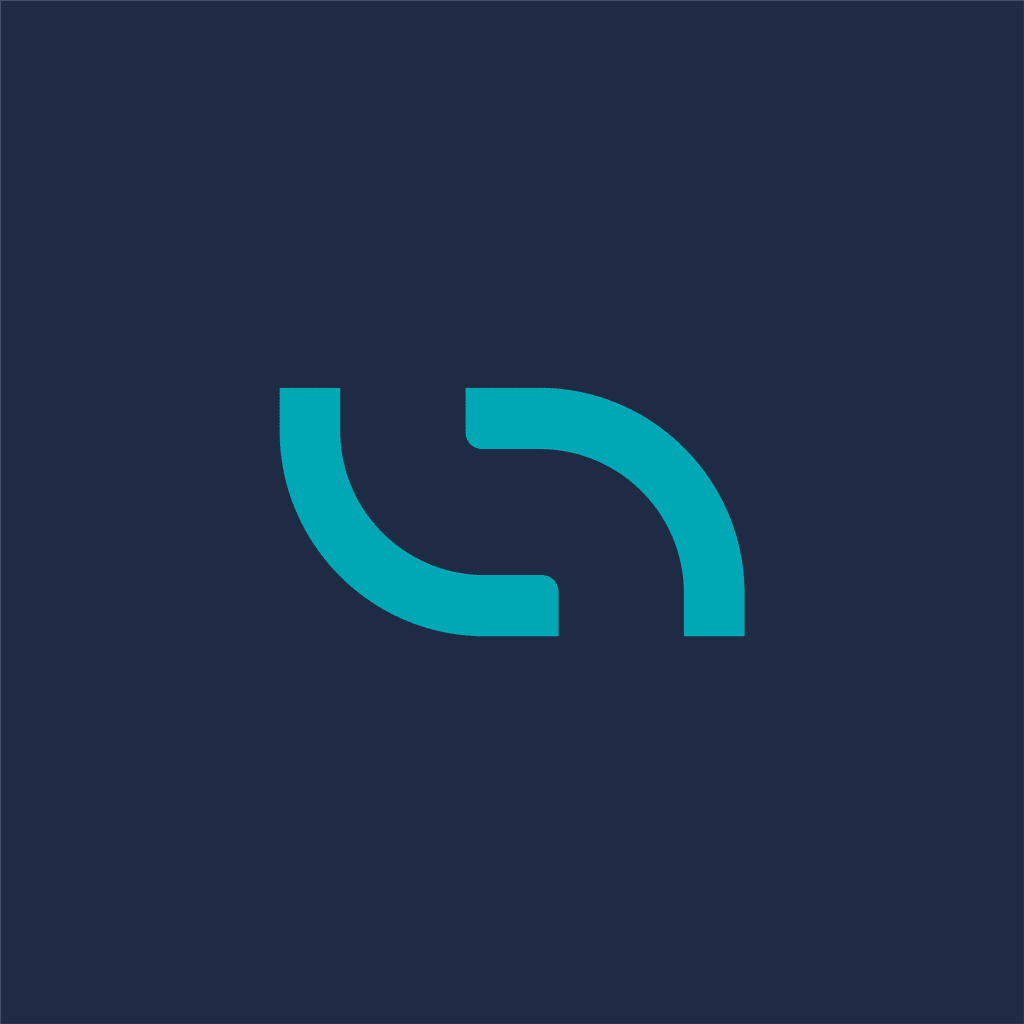
BOC praises 24-hour critical valve repair turnaround.
In the middle of February, BOC called us to investigate a recycle valve that was not stroking properly at its Worsley plant. This was a repeat problem which we’d previously resolved by adjusting the positioner. On this occasion when Field Service Technician, Jake Wood inspected the valve it was clear that the positioner needed to be replaced. Contracts Manager, Dave Morrison promptly contacted Project Engineer, Tracy Chapman in Gloucester who quickly advised us on several replacement options. One of these was already in stock in the Brighouse stores. So, Jake was despatched to BOC Worsley again the following day where he successfully installed the replacement part. This is a great example of multiple facilities collaborating to deliver a high level of customer service.
BOC praises 24-hour critical valve repair, as both the maintenance supervisor and the branch manager of BOC stated:
“I would just like to thank you for your quick response in getting our N2O filling system back up and running. This is a critical gas which we supply to the NHS and with your help and quick response we have managed to keep the supply chain going.” Mark Derbyshire, Maintenance Supervisor
“[You’ve] been a big help this week. Given the criticality of N2O, it’s prevented us having any immediate shortages to the NHS.” Dan Smith, Branch Manager
In the long-term the entire valve needs to be replaced, and Gloucester’s Tim Webb is on the case.
Severn manufactures and supports high quality valves for the energy industries. Its control, choke and small bore subsea valves are pre-eminent in the global market, underpinning the reliability and high performance of business-critical client infrastructure.
Severn’s global reach, technical prowess, and collaborative approach – all founded upon a heritage of British engineering excellence – help to assure production continuity for clients and reduce the prospect of costly downtime.
Its understanding of the life-cycle of assets positions Severn to offer end-to-end engineering solutions, enabling clients to meet their core imperatives: safe operations and minimum downtime.