Severn’s engineering heritage and excellence has led to the innovative design of a product that can master both Control & Isolation applications.
Utilising Severn’s long history with Control Valve design, our team of engineering experts have been able to manufacture a Triple Offset Butterfly valve that can be used to provide superior control in both throttling and modulating service, whilst additionally providing a repeatable seal for isolation duties.
By designing a Control Valve that can isolate, rather than an isolation valve that controls (which may initially sound the same but is vastly different), Severn have designed a Butterfly Valve that maximises the Cv with streamlined internals to provide optimal flow characteristics when controlling the process.
We have also eliminated the need to have fasteners on the disc or a bolted-on seal, thus enabling us to optimise the disc profile. Additionally, by removing fasteners from the disc, we have eliminated the risk of loose fasteners falling into the line due to vibration.
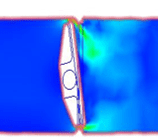
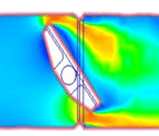
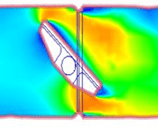
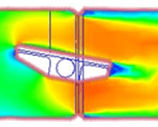
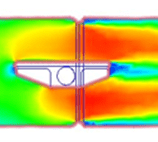
By adopting a body-mounted seal we have been able to increase longevity & reliability of the product. As we have taken this out of the flow path of line media, this reduces wear on the seal allowing Severn to maximise the bore size for an increased CV.
Using our Patented Oblique Cone Technology (OCT), we can also use circular sealing geometry which provides an even seal load around the circumference of the disc. This gives us repeatable bubble-tight sealing, improving product performance, reliability, and safety, ensuring you achieve your core remit of safe operations and minimum downtime.
The OCT geometry enables Severn to add an extensive range of trims to the valve not traditionally found on Triple Offset Valves. By utilising a one-piece disc, Severn can add anti-cavitation trims, when conditions dictate, to help control the flow. This can also be paired with baffle plates when needed, enabling a Butterfly Valve to be utilised when severe service conditions may mean a standard Butterfly Valve would not be suitable or would have a significantly reduced service life.
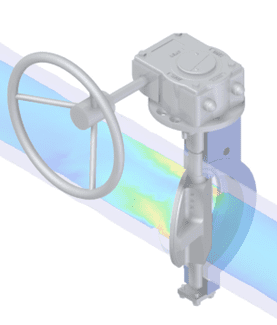
The OCT Triple Offset Butterfly Valve can be utilised for both control and isolation valve applications, enabling the end user to significantly reduce stock inventory and overall operating costs. Parts are standardised and interchangeable, meaning end users can have a reduced spares inventory leading to further cost reductions.
It also provides the end users with the option to potentially utilise one valve that can perform both the control and isolation functions within a system, rather than two – leading to significant reductions in operating and service costs and weight saving – this can be paramount for weight critical operations such as offshore installations.
Explore the design that has been inspired by engineering heritage and excellence to create a product that master’s isolation and control applications.
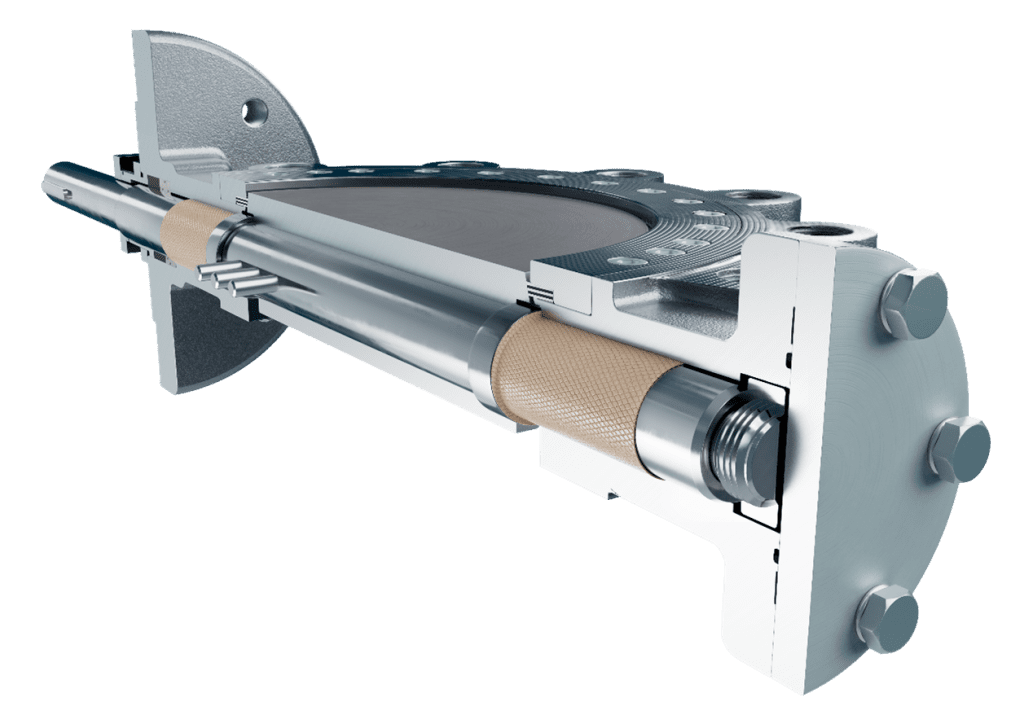
From the outset, Severn wanted the Oblique Cone Technology (OCT) to be unique in the Triple Offset valve market. Severn wanted to develop a product that not only solves an extensive range of issues for the customer with our “standard” product range, but to break tradition, and to design and manufacture a technically superior Butterfly Valve.
By utilising their comprehensive history with specialist butterfly valve design and manufacture, Severn have been able to develop a Triple Offset Butterfly Valve that performs both control and isolation duty in a single package. A valve designed from the outset to be re-used, upgraded, and provide an increased level of safety to the end user.
Severn have utilised its years of experience in manufacturing both the concentric and double offset Butterfly Valves to create innovative technology that pushes the boundaries of Triple Offset Butterfly Valve design. By looking at the traditional elliptical sealing concepts of Triple offset valves and combining this with circular sealing principals, Severn created its patented Oblique Cone Technology (OCT). In its most simplistic form, the geometry can be compared to a circular cone, by moving the point of the cone along one axis, this creates two different angles to the cone sides (forming an oblique cone), by taking a slice of this cone, it forms the sealing geometry of the OCT valve.
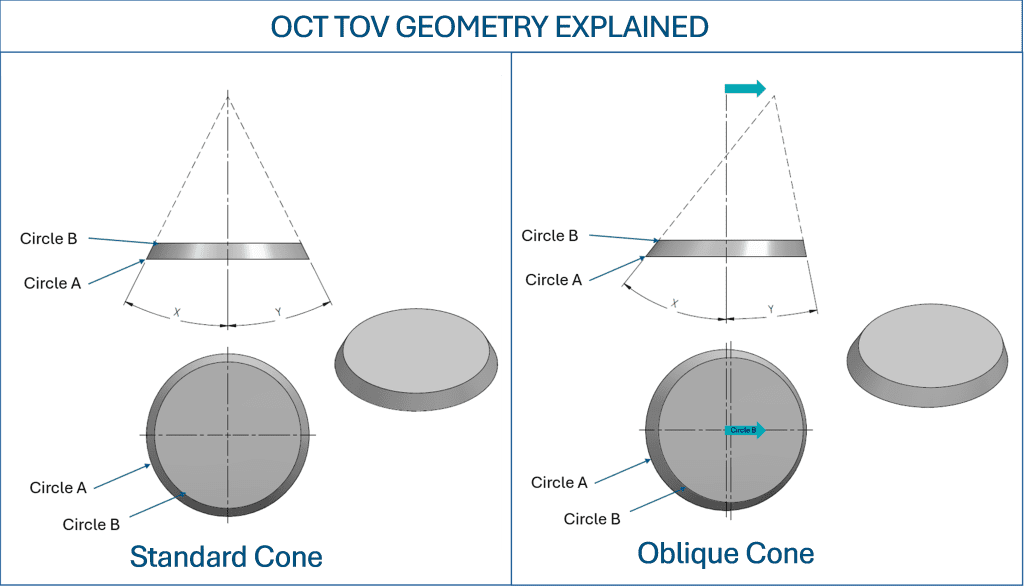
The benefit of this method means we maintain the principals of circular seals, thus providing an even seat load all-round the disc, therefore providing increased flexibility within the design to allow Severn to add different sealing options to the valve as well as specialist control trims such as anti-cavitation / low noise trims.
By understanding the foundational principals of Butterfly Valve design, Severn have a detailed knowledge of the interaction between each and every Butterfly Valve component. This combined with Severn’s Repair Intelligence philosophy and over 60 years of engineering excellence, customer solutions and end user feedback, problems can be anticipated and resolved before they occur and therefore increasing the lifecycle of the product and reducing costly unplanned downtime.
Severn additionally want to break the cycle of Butterfly Valves being a “throw away’’ commodity items. The OCT TOV Butterfly Valve is designed to be re-used, repaired, or upgraded on site with only basic tools. The robustness of the design means that the main components can be cleaned, soft goods replaced, and the valve can be reinstalled to provide extended years of reliable service. This not only reduces long term cost of ownership for the end user, but also reduces the environmental impact of the plant operations. Severn also install Fugitive Emission certified packing as standard in the OCT to further reduce the plant emission.
Flexibility and reliability come as standard in the OCT TOV Butterfly Valve. By using the principals of a Control Valve, Severn have streamlined and reduced the disc thickness to impede the flow as little as possible and maximise valve Cv. Fasteners have been removed from the disc, to eliminate the risk of them coming loose due to vibration and falling into the pipeline. The seal has also been mounted in the body rather than on the disc. This not only protects the seal by removing it from the direct flow path, but means the disc is thinner as well as giving Severn the option to add anti cavitation / low noise trims onto the disc when process conditions dictate.
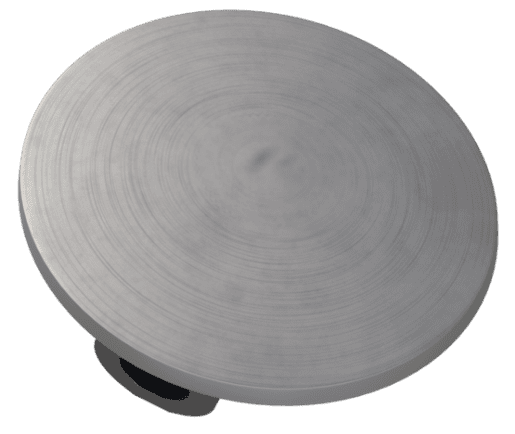
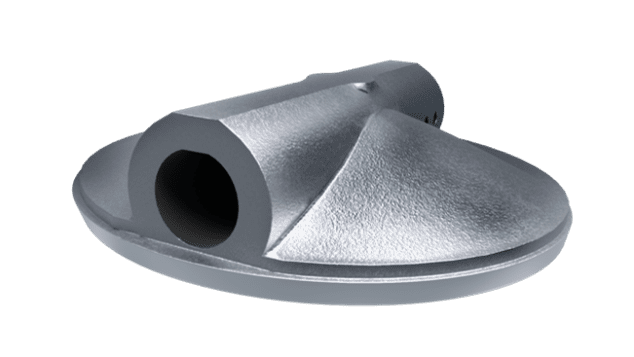
The OCT principle has been installed and operating in the field for over 10 years without issues, this coupled with countless amounts of testing and validation including fire testing, pressure testing, temperature testing and cycle testing, provide the end user with confidence in the robustness and reliability of the OCT Triple Offset Butterfly valve range and ultimately minimise down time and plant costs.

Compressor anti-surge control valves for FPSO North Sea Client delivered three days ahead of schedule
Compressor anti-surge control valves for FPSO North Sea Client delivered three days ahead of schedule
Compressor Anti-surge Control Valves delivered three days ahead of schedule
Industry : Oil & Gas FPSO
Location: UK Central North Sea
Project: Two anti-surge control valves to be delivered within a tight time frame for UK Central North Sea Client
The Challenge:
A North Sea operator needed a solution for a technically challenging anti-surge application, required on a very short delivery schedule of 16 weeks, the initial requirement was for one valve to be delivered and the second valve to be delivered 10 days later.
Finding a solution:
The Severn team made initial engagement with the client to full understand the application and performance requirements that the customer needed.
A swift coordinated approach internally by Severn’s application and engineering team was needed and the teams worked closely together as it was imperative that the issue was identified quickly so a solution could be provided, manufactured and delivered within the 16-week delivery schedule.
The product:
After identifying the clients requirements, the engineering team designed and manufactured two off 4” Cass 1500 RTJ Fig 5413 LTCS Body, SS/FC Trim, 14 Turn CCD, PC1N Pneumatic actuator with a Neles Positioner.
The positioner was revised mid order as per clients added operational requirements, the team was seamless in reacting to this change with no impact on the design or delivery schedule.
The outcome:
The contracts department managed the scope of the job and the challenges it brought professionally and with complete transparency; the client was kept fully informed throughout the production and delivery process.
The collaboration between the different departments and the constant engagement and the feedback with the client ultimately led to both valves being delivered three days in advance of the 16-week schedule, this was appreciated by the client.
The valve performed significantly well within the anti-surge required by the client for this application, especially on small step changes. This was a major issue with the clients previous valve, and an issue our team overcame with flying colours.
Severn requested to provide engineering support offshore on the asset, firstly with the installation and then subsequent valve commissioning activity.
” I want to take this opportunity to personally thank the entire Severn team for their continued focus and support during this project and more importantly, for getting both valves ready for shipping ahead of an already tight schedule.
Getting two high spec anti surge valves designed, assembled , and fully tested in less than 16 weeks is definitely an achievement” – Client representative
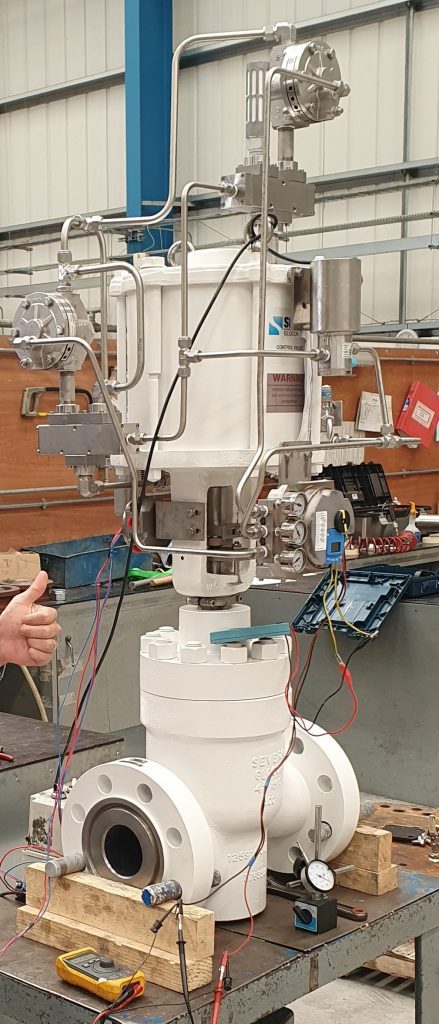