Shrewd Valve Engineering Solves Compressor Bypass Challenge
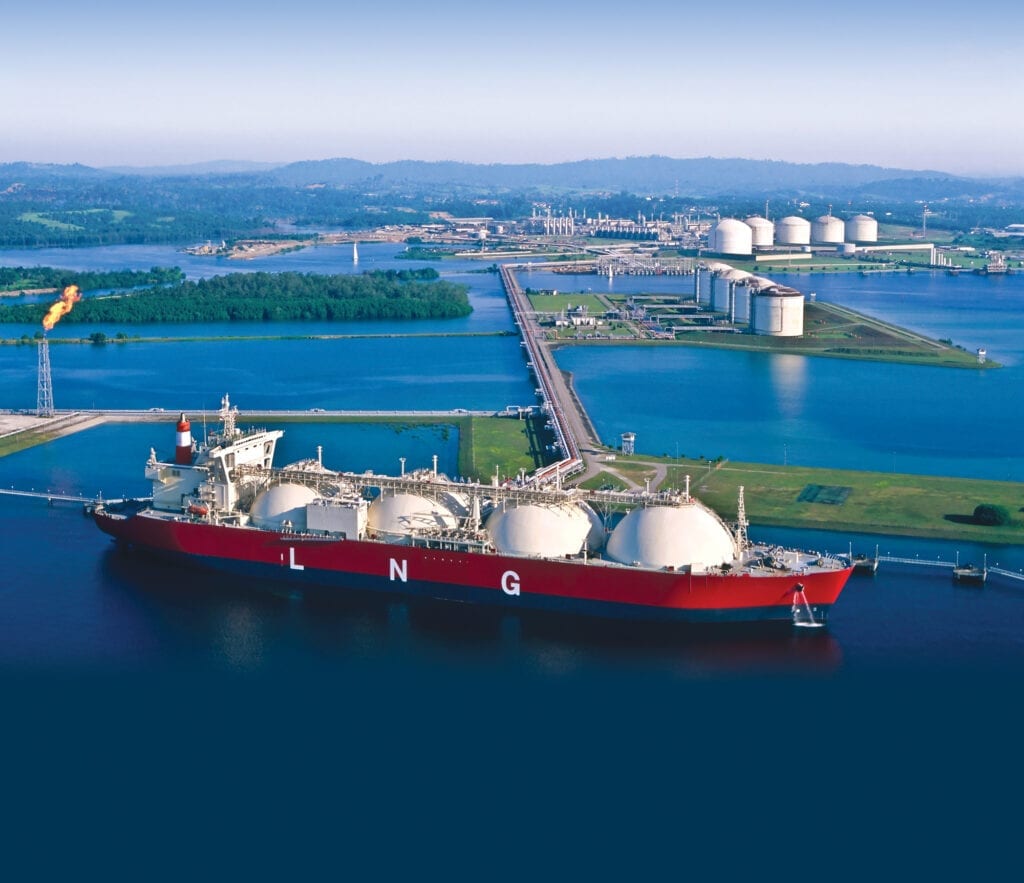
The Challenge
Compressors are one of the most critical components of an LNG train, both in terms of capital investment and operational costs. Their safe and sustained operation plays a vital role in strategies to maximise plant uptime and production levels.
It follows that valves deployed in compressor anti-surge and bypass applications need to meet the highest standards of performance and reliability. The rise of LNG megaprojects is compounding these challenges. Severn recently encountered an extreme specification for a compressor bypass control valve.
Rapid stroke time
The valve needed to stroke from fully closed to fully open across a distance of 18″ with a plug weighing more than 1 tonne in less than 2 seconds.
Velocity and pressure demands
The application involved the control of 3,784,320 Kg/hr of propane gas and required a 98% reduction in pressure (from 16.40 barg to 0.164 barg). This brought significant engineering challenges. As pressure drops, gas expands and its velocity increases. Careful management of velocity is vital since it has a direct impact on noise, which can cause vibration within the valve. Excessive vibration harms internal components and increases the risk of mechanical failure.
Low noise levels
Customer specifications demanded that noise levels should be lower than 82 dBa. Initial calculations indicated that in order to achieve this, velocity would need to be limited to 1/3 of sonic (0.3 mach). In order to meet the specification with a traditional control valve, an outlet of 64″ would be required. Such a valve would have been a global first, and the customer was reluctant to consider this option. An alternative approach was needed.
The solution
Core insight
Severn’s calculations revealed a core piece of insight which unlocked an innovative solution: while the noise reduction required a 64″ outlet, the flow coefficient could be controlled by a 36″ valve.
Innovative valve technology
The engineering team designed a 36″ angle valve fitted with a 2cc low noise trim. Then a 36″ x 64″ diffuser was bolted directly to the valve outlet. Three large steel baffle plates inside the diffuser control the flow, enabling outlet velocity to be maintained at lower than 0.3 mach. This enables the noise level to be managed at less than 82 dBa across the valve/ diffuser combination. To meet the demanding 2 second stroke speed requirements, the valve was packaged with a powerful, highly reactive actuator control system from STI in Italy
The outcome
Severn’s innovative response to the customer’s specification enabled a cost-effective, reliable valve solution to be developed. The result is a ground breaking valve technology that meets the extreme demands of the compressor bypass application while minimising long term risk and the initial capital outlay, shrewd valve engineering solves compressor bypass challenge.
Innovative valve / diffuser combination overcomes extreme LNG production challenge
If you want to read more of our case studies, you can find them by clicking the Case Studies button below or if you would like to contact us with an application, engineering or other valve query than click the contact us button.
Alternatively, you can download the full stage case study via the download button below.