Maintaining effective control of process media, whether in its liquid or gaseous form, is a fundamental concern for LNG operators. Many aspects of production depend on this, from ensuring operations are safe and environmentally sound to maximising output and profitability.
The performance of valves is central here. They play an instrumental role in critical phases such as liquefaction, as well as managing the velocity and pressure of process media and protecting high value assets such as compressors.
A strategic approach to LNG valve spares
LNG valves need to provide reliable, repeatable process control in a wide variety of process conditions.
Many applications involve extreme thermodynamics and pressure variations. This is accounted for in the selection of pressure-containing materials and the design of the valve trim (internal components which contact process media). Nevertheless, even the most highly engineered valves inevitably experience wear over time, and a plant’s entire valve population needs regular maintenance and repair. Maintaining a valve population is very much like a fitness regime: frequency leads to better health and efficiency which ultimately translates into better profitability.
Managing this effectively to ensure the right valves receive adequate attention at the right moment is crucial. It demands a robust maintenance routine, closely aligned with the development and implementation of an intelligent spares strategy. Upfront decisions have a significant bearing on this. Having operational spares available on site prior to the commissioning phase ensures unforeseen issues can be navigated to avoid any delay to start-up and commercial operation.
Getting the balance right is crucial; it can make the difference between enabling a continuous cycle of repeatable plant performance or triggering a downward spiral of decline. The latter leads to increased wastage, product/process variation outside acceptable parameters, lack of plant availability, unforeseen shutdowns and reduced profitability.
There is no simple one-size-fits-all solution. The unique circumstances and characteristics of the individual plant need to be considered. A plant like Yamal LNG, located within the Arctic Circle, is likely to have different operational challenges and priorities to Gorgon on Barrow Island. One faces extreme logistics challenges, constrained either by the ice road or shipping routes at different times of year and the other is situated within a Class A nature reserve in a sub-tropical zone. Factors like these influence operators’ priorities, which in turn impact best practice for valve spares.
It is important to give valve spares proper attention, so decisions are purposeful and considered. This is not always easy in the midst of a new project, when there are so many factors to consider and reams of paperwork to be reviewed. But creating time and space to consider spares at an early stage can save a huge amount of trouble further down the line. Understanding the different types of valve spares is a good place to start.
The three categories of valve spares
Valve spares encompass consumables, hard parts and associated instrumentation – we will look at the three categories in more detail shortly. A best practice approach identifies critical valves and applications, as well as general maintenance considerations, to ensure the right quantities and types of each category are held onsite.
The cost of procuring a certain type of spare should be considered alongside the potential repercussions of not having it when it is needed. In our experience, maintenance engineers tend to be more thorough and meticulous in routine valve inspections when they know a good stock of spares is held onsite. They are more inclined to open a critical valve, or a valve that isn’t quite performing as it should, at an earlier stage if they are confident that they will have the parts available to get it back online quickly if they find a problem.
Ultimately, this rigour enables engineers to identify and act on opportunities to prevent the escalation of emerging valve problems. Issues linked to subpar valve performance can range from tripping the plant to the damage of major pieces of equipment such as compressors, separators and pumps. Valve failure can also result in serious consequences that present danger to life. Any of these scenarios can result in lost production if the plant has to shut down, and there are significant financial penalties attached to fugitive emissions, health and safety breaches or an inability to offload or export.
When valve inspection or maintenance is delayed due to a lack of spares, vital opportunities to rectify issues at an early stage and avoid a disruptive event can be missed.
Consumable spares
A comprehensive stock of consumable spares is fundamental to rigorous and effective valve maintenance. Valve consumables include parts within the valve, such as gaskets, packing sets, metal seals and balance seals (depending on the valve design) as well as actuator repair kits. These parts all have a similar purpose, deforming under compression to form a seal. Any time a valve or actuator is opened for inspection, they must be replaced to ensure the integrity of seals is maintained.
Seals play a vital role keeping valves operational as leaks can be costly and, in some cases, they can seriously compromise health and safety. So it’s vital for any plant to have an extensive onsite supply of these items to avoid a scenario where engineers delay inspection because they do not have the relevant consumables.
It is imperative that OEM consumables are used as only the OEM knows the exact compression rates and critical dimensions to ensure a given part seals properly. Third party seals with incorrect compression or dimensions will result in leaks. This increases the risk of a negative environmental impact. Moreover, any upfront savings are a false economy if they lead to more significant costs due to damage from the leak paths that will occur.
Hard spares
LNG valves are often exposed to extreme operating conditions or circumstances that cause wear, erosion or corrosion over time. A valve’s internal trim is especially at risk.
Trim damage can also be caused by a variety of issues including, but not limited to, phenomena such as cavitation or flashing that can occur due to pressure let down or the inherent physical properties of flowing media.
The trim design of valves can be engineered to eliminate cavitation, but modifications to the surrounding pipework or evolving process conditions can introduce new vulnerabilities. Flashing cannot be eliminated, but materials are used to help the valve withstand it for as long as possible. Valves deployed in applications where flashing or cavitation occur should be subject to an enhanced maintenance routine. In this way, any wear can be identified and rectified at the earliest possible opportunity, before significant damage occurs and performance is compromised.
Noise levels are also a concern for certain LNG valve applications. Again, in most cases the trim design can eliminate or reduce the potential for this. However, sometimes noise that does not originate from the valve itself can have an impact. If a noise issue is identified, valves need to be inspected as soon as possible since the associated vibration can cause catastrophic damage to a valve’s internals.
Trim spares typically include the plug (usually an assembly of the stem and plug head), seat and cage. Different operators use different terms for the cage – essentially, it is an internal component that can perform multiple roles in the control of the process medium. These can include control of pressure let down and outlet velocity, as well as provision of valve characteristics such as linear or equal percentage etc. They can also clamp the seat in place and protect the plug.
Additional hard spares include gland followers and guides (also called stem guides or guide bushes, depending on the valve design). Some valves also require retainers, especially if a soft seat and/or balance seal have been installed. In some valves, integral seat diffusers or liners protect the valve body from the exit velocity of the trim.
As with consumables, when third party spare parts are used the operator carries the burden of the valve warranty being invalid and takes ownership of the valve. OEM parts are always preferable. They are manufactured to exacting critical dimensions that only the OEM fully knows and only the OEM can ensure support for the duration of the valve’s life. In certain circumstances – especially those relating to the key elements of a plant – use of third-party spares can invalidate the plant’s insurance.
Understanding which valves are likely to experience problems resulting from issues such as flashing, cavitation and noise is key here. By ensuring relevant replacement parts are stocked onsite, engineers are given greater freedom and autonomy for preventative and corrective maintenance. This is a fundamental aspect of continual improvement. The alternative is to risk delaying inspection and maintenance, which can result in subpar valve performance hindering production levels. In the worst cases, this can cause irreparable valve damage leading to an extended or unplanned shutdown.
For some operators, this risk is untenable, and a decision is taken to hold whole valve spares onsite for certain high-risk applications. This ensures that if a valve requires attention, it can quickly be taken offline and switched for the spare valve in the minimum amount of time to get the plant up and running again. Once the original valve has been removed for a complete overhaul, with parts replaced (ideally from the stored stock) or repaired as necessary, it is held as the spare in case of any future issues. This is not an uncommon scenario on LNG plants with multiple compressor trains.
Instrumentation
Valve instrumentation devices – such as positioners, air filter regulators, solenoid valves, lock up valves, pilot valves, volume boosters or quick exhaust valves – are typically mounted on the actuator. This makes them vulnerable to damage, both during installation and operation. They are also exposed to the elements, so they are susceptible to damage caused by humidity, ice, insects or sand depending on the plant environment.
Since valves cannot function without these devices, best practice dictates that an optimised stock of complete units is held onsite.
A tailored approach
Ultimately, a valve spares strategy must balance the available budget against the potential production losses if a valve performs badly or has to be taken offline. There is no perfect solution to this challenge, but with a considered approach it is possible to manage risk effectively and ensure optimum process control is maintained.
A detailed appraisal of critical and severe service LNG valve applications combined with an understanding of the plant’s unique circumstances and characteristics provides a solid foundation. This is where it can be advantageous to draw on specialist third party support guided by a Spare Parts Interchangeability Record (SPIR) to ensure optimum stock levels. It empowers maintenance engineers to work with confidence, taking proactive steps to keep valves in good working order to ensure continuity of plant availability and performance.
HIPPS (High Integrity Pressure Protection Systems) are rapidly gaining ground in the LNG sector as an alternative to pressure relief systems. Situated between high-pressure upstream and low-pressure downstream sections of an installation, they contain media if over-pressurisation is likely to occur.
The core benefit of HIPPS is that the system is activated before over-pressurisation, automatically bringing high-risk processes to a safe state. With traditional pressure relief systems, a relief valve is triggered to vent during over-pressurisation. This allows excess gas or fluid to escape into the surrounding environment.
Superior downstream protection
A HIPPS is a sophisticated valve-based safety instrumented system (SIS) designed to protect equipment from over-pressurisation scenarios that could result in full emergency shutdown. These systems offer superior protection of downstream assets on any LNG plant, vessel or facility.
Traditionally, installations facing the strictest environmental regulations were at the forefront of HIPPS uptake as the systems out-perform standard safety regulations. However, associated economic advantages are now more widely recognised and driving further interest.
As an emergency response solution, HIPPS deployment is far less costly than lengthy emergency shutdowns and all the repercussions they entail. When a relief valve is activated, operators face heavy costs surrounding intervention and lost production. But the benefits of HIPPS go further than simply reducing costs in the event of an incident. Deploying HIPPS in a pipeline unlocks the potential for lower downstream design pressures. So, the required wall thickness for downstream assets decreases, allowing de-rated pipework to be used, which brings potential size, weight and cost advantages, as well as having a positive impact on flow rates and throughput.
So, while environmental requirements initially drove LNG HIPPS uptake, it’s now widely recognised that there are three scenarios where the systems should be brought to the table. If the surrounding environment needs to be protected, the economic feasibility of a development needs to be improved or the risk profile of a facility needs to be reduced, HIPPS is an attractive and viable alternative to simple relief systems. HIPPS are equally effective in new projects or when adding to or upgrading existing installations.
The art of HIPPS integration
HIPPS have a high degree of redundancy to maximise safety for site personnel, the general public and the environment, as well as high-value production assets. They are comprised of integrated technologies arranged in a complete functional loop, with three fundamental components:
- Pressure Transmitters monitor pipeline pressure and convey a signal to a logic solver.
- The Logic Solver captures signals from the pressure transmitters and performs a 2oo3 voting logic.
- The Final Element (normally two shut-off valves) provides corrective action to bring the process to a safe state.
This configuration maximises performance and reliability. The 2oo3 (two out of three) methodology enhances the systems’ ability to detect problems, while reducing the likelihood of a response being triggered unnecessarily. Should one of the pressure transmitters fail, it won’t compromise functionality as two high pressure readings are required for activation. Likewise, if one of the valves in the final element fails, the second valve acts as a back-up to maintain the isolation of the high-pressure source.
Clearly, in an ideal world, safety systems would never need to be activated. Plant designers and engineers should continually strive for inherent safety. HIPPS are the last line of defence and shouldn’t be considered an alternative to designing out potential over-pressurisation problems. Holistic thinking and intelligent design reviews are essential to enhance overall safety and get the most out of HIPPS.
Front-end planning
When projects don’t allow adequate time for detailed assessment upfront, it can result in the installation of HIPPS with an inappropriate safety integrity level (SIL) specified. On an existing plant, this can result in continued reliance on emergency shutdown valves or a failure to realise the full benefits of HIPPS. Ascertaining the correct SIL assignment at the outset is a critical success factor, and it should be a core driver for system design and decision making.
Engaging a HIPPS integrator at an early stage is another crucial step. Ideally, they should be independent, so they have the freedom to draw on the best technologies to meet specific needs of an individual plant application. And they should offer a good depth and breadth of specialist HIPPS expertise so they can devise innovative approaches with a superior level of reliability. For instance, the expert selection of components from various manufacturers can reduce the potential for a ‘common cause factor’ resulting in system failure. It is established good practice to use two valves in the final element of the loop to enhance redundancy. But in many cases two valves of the same type from the same manufacturer are deployed. Opting for two different valve designs, such as a gate valve and a ball valve, from independent suppliers is a more effective way to maximise redundancy, enhancing overall safety and reliability.
There’s no denying that the deployment of HIPPS can complex and challenging. To counter this, their development and integration should draw on the combined expertise of electronic and software engineers as well as mechanical engineers. These experts need to work cohesively with functional safety management professionals to interrogate the design brief and look in detail at SIL requirements. Typically, an independent integrator will employ all these professionals in-house. They will also have a robust functional safety management system in place, as well as a competency management system ensuring people are trained and certified to exceed the relevant industry standards.
A further benefit of this model is that all the requirements of HIPPS integration can be put in place via a single point of contact. This eases communication throughout planning, development and delivery, and enhances efficiency by stripping out a layer of third-party liaison and coordination. What’s more, external professional consultation can support the project in a validation role at specific milestones. This consultative ‘one-stop-shop’ approach makes for a structured, cost and time saving solution.
Collaboration between the end user and an independent HIPPS integrator facilitates the creation of an innovative and effective long term solution. Opting for best-in-class, expert-led protection of equipment that could be susceptible to over-pressurisation brings multiple benefits.
The eight phases of HIPPS
Each phase of a HIPPS project is dictated by safety lifecycle standard IEC 61511, including decommissioning at end of life. A partnership approach with clearly defined responsibilities enables operators to benefit from the specialist expertise of HIPPS integrators and other third parties.
- Hazard and risk assessment or Hazard and operability study (HAZOP) (end user responsibility)
- Allocation of safety functions to protection layers (end user responsibility)
- Safety requirements specification (end user responsibility)
- Design and engineering of safety instrumented system (HIPPS integrator responsibility)
- Installation and commissioning (HIPPS integrator responsibility) followed by validation (certifying body responsibility, e.g. TUV)
- Operation and maintenance (end user and HIPPS integrator, shared responsibility)
- Modification (HIPPS integrator responsibility)
- Decommissioning (end user and HIPPS integrator, shared responsibility)
Application spotlight: FSRU HIPPS
Engineers from Severn recently integrated, supplied and commissioned a HIPPS for an LNG Floating Storage and Regasification Unit (FSRU) being built by DSME in Korea.
The vessel, BW Magna, has a 173,400 cubic metre capacity and the HIPPS has been installed to protect the pipeline during the unloading of gas. This enhances safety for the FSRU itself, as well as the downstream equipment and pipeline in the docking terminals it connects with.
HIPPS are not mandatory on FSRUs, but it’s increasingly recognised that they provide a superior level of safety and reliability. The system supplied to DSME operates at a working pressure of 117 barg. It comprises two 18” 900-class manual valves, a Sella Controls logic solver and three pressure transmitters.
Additional safety measures on the FSRU include alarms, a shutdown system, blow down system and safety valves, as per industry-specified standards. The benefit of adding HIPPS is that it is a simple, proven solution which can operate independently of the wider vessel system.
Conclusion
The design, build and testing of HIPPS poses many challenges, compounded by a lack of defined standards for design parameters. This calls for a high level of interaction between the end user, HIPPS integrator and other parties throughout the eight phases of HIPPS development and deployment. However, the investment of time, money and effort reaps dividends in the shape of superior safety and environmental credentials combined with associated economic advantages. These three factors are coming under increasing scrutiny in all areas of the energy industry. LNG players who invest in the best safety systems now will be one step ahead.
Stringent Anti-Surge Valves specifications can pose challenges for larger valves on LNG liquefaction trains. But Severn’s bespoke Anti-Surge Control Valves ensure efficiency and compliance.
LNG compressor manufactures are placing increasingly stringent performance requirements on Anti-Surge valves, and specifications are often written without considering valve size. Yet while the standards are easily achievable for smaller valves, they become significantly more difficult as valve travel (the distance the plug moves) increases. Since specifications are primarily based on safety and efficiency requirements, any deviations introduce risk; concessions are not generally accepted.
Technical challenges for large Anti-Surge valves
Fundamental principles of physics make it harder for larger valves to achieve the optimised, highly efficient control required in Anti-Surge applications. The weight of the valve plug and the long linear stroke of the actuator introduce mechanical inertia and lag, which can result in a slower or more erratic valve response. Consequently, to ensure safety, end users have traditionally had to tolerate a conservative approach to surge control when using larger valves. This compromises overall system efficiency.
Severn’s Anti-Surge Control Valves are engineered to overcome these challenges, and we recently put a 30” test specimen through its paces with dynamic testing. Results prove that even large valves commonly found on LNG mega trains can fully comply with rigorous compressor manufacturer specifications.
Dynamic testing explained
Dynamic testing for Anti-Surge valves determines how a valve performs when subjected to operational parameters that will be encountered on the liquefaction train. Speed, precision and stability are the critical features evaluated.
Assessing speed of response
Anti-Surge valves must react quickly via automatic control when an imminent surge event is detected, and the control signal is activated.
Compressor manufacturers’ dynamic testing parameters specify a maximum time from cut off (i.e. when the valve is fully closed) to fully open. This is typically around 2 seconds. Another specified parameter is the time taken for the valve to move from cut off to 80% open. The target timeframe for this is generally 1.5 seconds.
Opening time specifications are inclusive of dead time (the delay between the control signal being sent to the valve and the beginning of the valve response). It’s common for dead time to be allocated its own required value. For instance, the preferred time might be 0.3 seconds and the maximum allowable time 0.5 seconds.
Validating precision control
When a valve’s ability to quickly achieve the ‘fully open’ position is critical for safety, it is only necessary in emergency surge prevention situations. Much of the time a surge event can be avoided via carefully modulated control of the Anti-Surge Valve. In fact, opening too far may result in an excessive amount of compressed gas being recycled, which is wasteful and harms efficiency.
That’s why dynamic testing also assesses a valve’s ability to achieve precise movements without too much overshoot (when the valve moves more than required) or stiction (when plug travel is jerky due to friction). Proving that any overshoot or stiction are minimal provides assurance that the valve can achieve accurate, precision control.
Take the Baker Hughes dynamic testing specification. This compressor manufacturer describes one test for valve moment involving continuous changes in the control signal from ‘98% opening’ to ‘2% opening’ over a five-minute period. Stiction of less than 1% is preferred, and the maximum allowable stiction is 1.5%. In other words, the test looks to identify whether friction causes any significant deviation between input signal and the valve’s position.
Demonstrating Stability
As well as maximising efficiency, smooth operation of Anti-Surge Control Valves is vital to avoid compressor surge being caused inadvertently.
Oscillation (repeated overshoot and correction), or the use of extra force to overcome stiction, can destabilise the compressor, pushing it into surge rather than avoiding it. What’s more, a valve that responds too aggressively to small, high-frequency signal variations may be overly sensitive to noise and mechanical vibrations in nearby equipment, including the compressor. If the valve moves unexpectedly and unintentionally due to environmental factors, resultant pressure fluctuations could be hugely detrimental to compressor performance and the wider liquefaction process.
Frequency response testing plays a critical role here. It shows how quickly the valve opens and closes in response to control signals at different frequencies, identifying whether it overshoots or oscillates. Tests demonstrate the sensitivity and linearity of the valve and actuator assembly, showing whether they respond accurately to small control inputs.
Bigger valves, better control
The 30” Anti-Surge Control Valve demonstrated exceptional speed, precision, and stability in dynamic testing. Results show that our bespoke valve design coupled with sophisticated actuation allows large valves to operate reliably and safely within a centrifugal compressor’s maximum efficiency zone.
Severn’s experience supplying technically challenging control valves for critical equipment enables us to meet customers’ safety and efficiency requirements without compromise. Check out our previous articles which look specifically at the customisation of valve trims and control optimisation to facilitate this high level of performance. Or contact us to find out how valve engineering expertise can benefit your LNG project.
Large LNG compressors require large Anti-Surge Valves which in turn present complex engineering challenges. Valves with shorter travel (the distance the plug moves) and suboptimal control compromise the efficiency and reliability of the compressor. But traditionally, it’s difficult to control valves with a long stroke involving more than 12” of travel.
With extensive experience developing Anti-Surge Valves, Severn resolves these challenges. Our expert valve selection, integration, setup and calibration enable large valves with up to 24” of travel to meet stringent performance and safety specifications.
Anti-Surge control valves must act extremely fast – within a two-second window – when process upset is detected on an LNG liquefaction train.
To facilitate a rapid inflow of surge gas, these valves typically have an oversized capacity of 1.8-2.2 times the maximum volume they are likely to handle. However, this important safety feature has implications for valve size, weight, and travel.
It is harder for large Anti-Surge valves to achieve the balance of speed and precise control required for compressor protection and optimal flow management. To compensate for this, LNG surge management systems involving large valves are often configured so that valves are activated at a lower threshold. This approach ensures plant safety, but it can compromise plant efficiency.
The whole valve package: focusing on the trim, actuator, and positioner improves operability
Severn’s proven Anti-Surge Control Valve technology takes a complete, highly engineered approach to overcome performance challenges for optimally selected valves where travel exceeds 12”.
Our bespoke valve trims for precise pressure let down, are integrated with sophisticated, carefully selected actuators and positioners. The impressive power and controllability of the actuation package is an integral feature of our valves. Precision control is enabled using high-power piston actuators which ensure a rigid and robust instrumentation setup. This enables us to implement a longer stroke – giving better control of the surge management process – while meeting the application’s exacting requirements for speed and accuracy.
The entire valve assembly is expertly integrated and calibrated as a complete system to deliver optimum performance. Valves are tested using a Profiler tool which measures and validates performance according to the specific Anti-Surge specifications. The tool is independently calibrated, ensuring valve performance is verified against end user standards without concession.
Our experienced valve engineers leverage test outcomes to fine-tune the actuator, positioner and boosters. Treating the Anti-Surge solution as a system of carefully selected, finely orchestrated components facilitates optimised, compliant valve performance.
Control optimisation boosts LNG productivity and efficiency
As the below graph indicates, when compressor Anti-Surge Valves are primed for speed, accuracy, and reliability, liquefaction trains can operate within the compressor’s maximum efficiency zone. The entire LNG plant benefits from this. Controlling surge quickly and safely without it escalating into a major event allows operators to maintain higher liquefaction flow/pressure rates which boost overall productivity.
GRAPH IMAGE
Severn’s Anti-Surge Control Valve technology enables this balance of speed and accuracy to be achieved consistently, even with large valves. With our ongoing commitment to R&D, Severn carried out stringent Anti-Surge specification testing on a valve with a nominal bore of 30” and a linear stroke of 24”. It performed the full 24” stroke in less than two seconds and achieved incredibly precise positional control ensuring specifications can be met without concessions on all valve sizes.
Contact us to find out more.
Bespoke trim designs optimise compressor Anti-Surge valves for the specific application demands of the LNG plant where they’re installed.
Internal components of a valve that come into contract with process media – collectively known as the trim – are critical to its reliable operation. This is especially true of Control Valves that protect centrifugal compressors from surge events on LNG liquefaction trains.
Compressor Anti-Surge Control Valves are often exposed to high flow velocities. Severn’s Repair Intelligence data (based on our engineers’ analysis of historic OEM valve products) shows this can lead to severe operational issues including high noise levels, vibration, erosion, and premature failure. These problems bring the risk of safety issues, production loss, and unscheduled shutdowns. Spiralling costs can be incurred too, due to frequent maintenance and replacement of damaged parts.
Since process conditions vary considerably between LNG projects, tailoring compressor Anti-Surge Valve trims to handle specific gas flow characteristics is highly advantageous. As well as facilitating precise and reliable control, this enhances valves’ ability to endure the operating conditions, improving longevity and reducing potential maintenance and safety concerns.
Customising valves for endurance and performance
To enable the release of process gas, Anti-Surge Valves are sized (as per specification) to have 1.8-2.2 times the required capacity for the process conditions. This ensures enough gas is supplied to the compressor to prevent surge and avoid a trip situation. Due to the high velocities created by the process, the gas must be carefully controlled, and the trim fulfils two main duties. The first is to enable the controlled release of the process gas that can cause the compressor to go into surge. The second is to control the velocity of the gas passing through the valve.
As well as having potential to cause erosion, the velocity of the gas can result in high aerodynamic noise levels which may exceed acceptable plant limits. High noise levels are also indicative of vibration within the trim which may affect the valve and downstream equipment, potentially inducing various modes of failure. Lagging the pipework is often seen as a solution, but this does not address the root cause. It is more effective to optimise the valve trim for the process conditions.
Severn’s bespoke trims optimise surge gas control
Severn’s Anti-Surge Control Valves benefit from engineered solutions to address the high capacity and velocity control requirements of the application. Trim components that benefit most from engineer-led customisation are the plug and the cage.
Precision engineering of cage geometry, informed by Severn’s expert analysis of flow conditions and Repair Intelligence insights, improves valve responsiveness and overall control. For instance, the 3D flow path of the cage can be engineered to reduce deadband and improve controllability. Our Multi Labyrinth Trim (MLT) can handle up to 48 stages of velocity reduction and our 1CC trim offers a high-capacity option which maximises throughput. To balance the need for high capacity and precise velocity control, we have also developed the Vari-Stage Trim which can be configured to meet end users’ exact process requirements.
A valve’s cage helps to balance pressure and reduce turbulence as the plug lifts and surge gas enters. Even so, there can be a delay in the equalisation of pressure in the area above the plug with the changes below it. This can lead to severe vibration and instability if the system does not respond in adequate time.
Severn’s Repair Intelligence has identified that process forces acting on a valve plug can severely detract from valve performance in operation. To combat this, we have developed a ‘Waggon Wheel’ plug design, in addition to our standard options, which can be implemented where conditions dictate. The design ensures process forces are equalised across the plug allowing for rapid movement and accurate control.
All these solutions are designed and engineered using Severn’s robust sizing and selection process, technical expertise, and years of Repair Intelligence.
Valve engineering expertise
Severn’s Anti-Surge Control Valve Technology is rooted in an adaptive design process led by experienced engineers. Applying our valve engineering expertise to compressor Anti-Surge challenges on an application-by-application basis results in durable, highly functional valves which ensure reliability, efficiency and safety.
Contact us to find out more.
Sophisticated Anti-Surge valve technology from Severn leverages advanced actuation capabilities to deliver precision control, maximising LNG plant efficiency, safety, and productivity.
Controlling centrifugal compressor surge is a fundamental aspect of efficient LNG production, and Anti-Surge Control Valves play a vital role.
Surge events can damage critical rotating equipment, harm plant performance, and result in costly unplanned downtime. Yet a conservative approach to surge risk management compromises plant efficiency and productivity by constraining the compressor’s operating envelope. Identifying an acceptable trade-off between these two extremes is increasingly difficult as trends in LNG production evolve.
The escalating challenge of LNG surge control
Challenges surrounding compressor surge control have become significantly more difficult in the quest for optimised efficiency. With global demand for LNG growing, the capacity of existing and future ‘mega trains’ is increasing. This requires larger valves sizes, which makes it harder to achieve fast, accurate control in anti-surge applications.
Surge events can occur within milliseconds and without warning, meaning Anti-Surge Control Valves must operate with exceptional speed and precision. However, fundamental principles of physics and engineering make it harder to achieve critical performance parameters as valve size increases. The mass of larger valves introduces greater mechanical inertia, so more force is required to control the travel of the plug (the main moving part). Handling larger volumes of gas also introduces significant dynamic inertia and pressure delays, further impeding valve response times.
On LNG plants where Anti-Surge Control Valve travel exceeds 18”, operators traditionally had to tolerate conservative surge control measures, compromising overall plant efficiency. Until now…
Raise the surge control line, boost efficiency
Severn’s latest innovation addresses issues associated with larger Anti-Surge Control Valves head on. Our engineers have applied their technical expertise to the development of a robust, highly engineered solution.
Benefits include fast operability, high controllability, excellent reliability, and extremely accurate valve control. This means the valves respond very quickly (in less than two seconds, including any deadband), without compromising controllability when surge is imminent. As the below diagram shows, these superior performance characteristics enable centrifugal compressors to operate closer to the surge control line, optimising performance and efficiency.
Severn recently completed testing on a proof-of-concept Anti-Surge Control Valve with a nominal bore of 30” and a linear stroke (the distance the actuator travels) of 24”. The valve specimen’s pressure rating was ANSI 150, and it was designed with a flow coefficient (Cv) exceeding 7700, in line with the process conditions of a typical Anti-Surge application.
Testing showed that the valve meets all required parameters of the world’s most stringent Anti-Surge specifications. A significant highlight was its ability to perform the full 24” stroke in less than two seconds while simultaneously achieving incredibly precise positional control. The exceptional performance enables accurate and reliable control close to the compressor surge control line, striking an effective balance between safety and efficiency without concession or compromise.
There is a great variation in centrifugal compressor process conditions, in terms of feed gas properties and operating parameters such as flow rate, pressure, and temperature. It follows that Anti-Surge Control Valves must be individually specified and designed to optimise compressor performance and, in turn, maximise LNG plant performance and efficiency. Future articles in this series will explain how technical aspects of our Anti-Surge Control Valve technology, such as control optimisation and trim design, are customised to meet specific application needs and requirements.
Meanwhile, if you’re looking for expert technical input on centrifugal compressor surge control or other severe or critical service LNG valve applications, contact us at sales@severnvalve.com
Severn has a strong track record in the design and manufacture of valves that overcome the most challenging technical issues. LNG projects we’ve supplied in the past include Ichthys and Gorgon.
With their direct influence on safe, economical plant performance, compressors are a vital component of the LNG liquefaction train. Protecting them from the ‘surge phenomenon’ helps avoid costly damage and unplanned downtime.
Centrifugal compressors are critical to LNG production, raising the pressure of feed gas so it meets the thermodynamic requirements of liquefaction. Highly engineered and complex in nature, they are also expensive – typically costing millions of dollars.
Under normal process conditions, the impeller within a centrifugal compressor rotates at high speed accelerating the flow of the feed gas. It’s important that the inlet flow rate is sufficient to maintain this forward movement and keep the gas flowing along the liquefaction train. However, changing process demands across the wider system can cause fluctuations, bringing the need for extremely fast and accurate mitigation measures.
What is ‘compressor surge’ and why must it be controlled?
The surge phenomenon occurs when inlet flow stalls because it is insufficient to overcome the high pressure at the compressor’s discharge point. This results in a reversal of flow which can trigger a surge cycle: compressed gas rushes backwards through the impeller, reversing the flow direction of the gas and thus reducing discharge pressure and potentially stalling the compressor. As discharge pressure lowers, forward flow resumes, only to be reversed again.
Compressor stall and surge events happen within a 20 – to 50-millisecond window without warning and, if left unchecked, a surge cycle will continue indefinitely. The extent and immediacy of any consequences depends on the frequency and power of the surge force, the vibrations it generates, and the temperature of the surging gas. Associated risks range from short-term performance issues to catastrophic failure of the compressor and lengthy, costly unplanned downtime.
LNG project owners and engineering, procurement, and contractors (EPCs) need to consider the following factors when making decisions about surge control:
- Surge damages the compressor, compromising performance
A surge can damage compressor seals, with their replacement costing tens of thousands of dollars. Surges can also cause significant mechanical damage to bearings, the impellers or the shaft, and other critical components. As well as hindering the plant’s operational efficiency, a damaged compressor is more prone to leakage, posing a serious risk to safety and the environment.
- Consequences of compressor surge can lead to LNG plant shutdown
Stable operation is vital to the safety and efficiency of an LNG liquefaction train. Flow reversal can lead to major process-related problems requiring emergency shutdown. The repair or replacement of damaged compressor components can also necessitate downtime. Unplanned LNG plant shutdown has a major impact on production. It can lead to significant financial losses, possibly up to tens of millions of dollars, further highlighting the critical importance of a fast, accurate solution.
- Minimising the gap between ‘surge’ and ‘surge control’ maximises plant performance
Reducing the likelihood of compressor surge is critical. Yet, while a surge event can have serious consequences, an overly conservative approach to surge risk management constrains the compressor’s operating envelope, limiting overall plant efficiency. Effectively balancing risk requires a range of measures, from fast, accurate, dynamic control systems to predictive analytics and regular maintenance.
Severn has the solution to the enduring surge control challenge
Severn has engineered a sophisticated Anti-Surge Control Valve solution with advanced actuation capabilities to overcome this enduring challenge of LNG production.
Severn brings extensive experience in the design and manufacture of LNG valves for both the cryogenic and liquefaction phases of production. Previously, we’ve supplied severe and critical service valves for LNG liquefaction projects such as Gorgon and Icthys.
Contact us to find out how we can support your LNG development goals.
With a few weeks until IEW 25, Severn, a renowned leader in fluid control solutions, is thrilled to introduce the dynamic team of valve experts who will be representing the company at IEW 25 in Delhi from the 11-14 February.
As the world gears up for one of the most significant gatherings in the energy sector, Severn’s selection of experts promises to elevate the discourse on cutting-edge valve technology and innovation.
Join us as we unveil the names and expertise behind Severn’s delegation, offering a glimpse into the exceptional insights and knowledge they will be bringing to IEW 25.
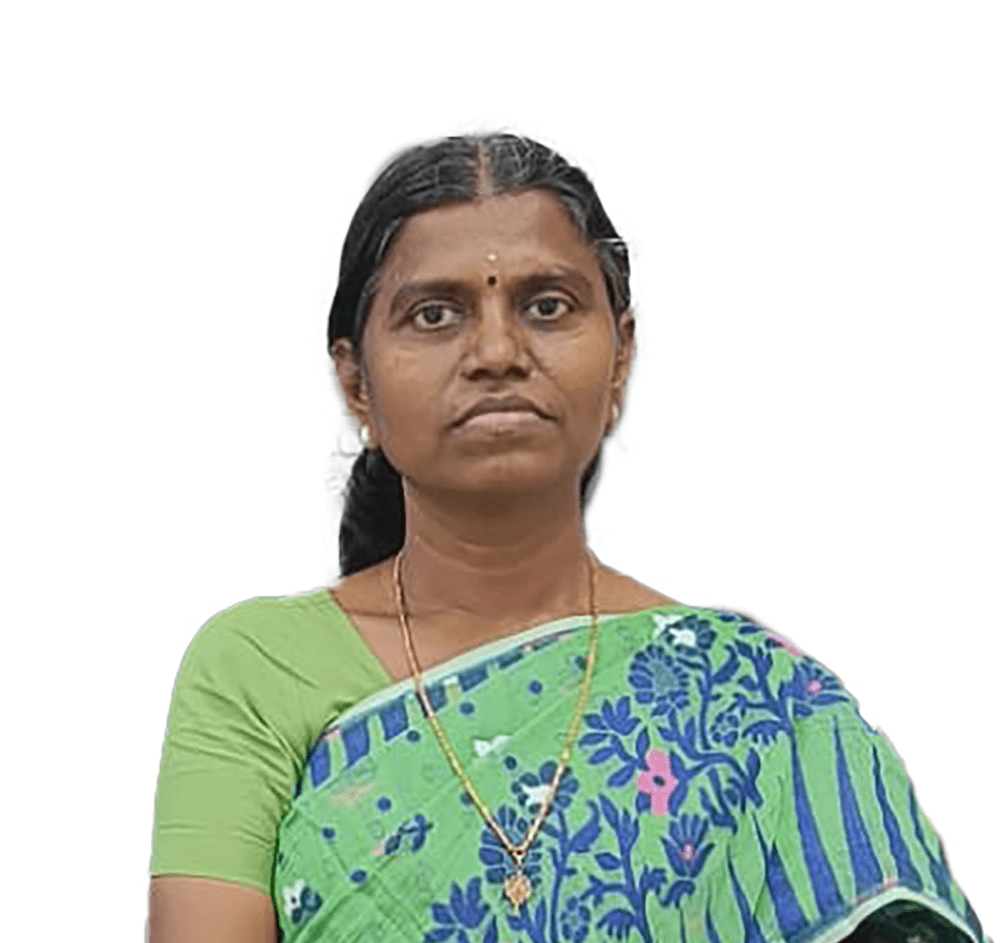
Malathy – GM – Application Engineering – Oil & Gas, Offshore, FLNG, FPSO, FSRU
With over 19 Years of experience in the Oil and Gas Industry (specialising in Upstream & FPSO), Control Valves and Chokes with broad and specialised technical knowledge. Malathy brings a whole range of skills to the IEW team such as professional approach, decision-making, problem-solving, interpersonal skills, etc.
Alongside technical expertise, Malathy also has fantastic commercial acumen, winning large project orders, handling complex projects that involve new design and developments, special materials, quality, validation testing, etc., and possesses good exposure to International Standards (API, ASME, ISA, ASTM, and other relevant standards).
Malathy is currently working to expand the supply base of Severn products globally, especially in Southeast Asia, the Middle East Market, South America, Africa, etc., and is a fantastic addition to the Severn IEW 2025 team.
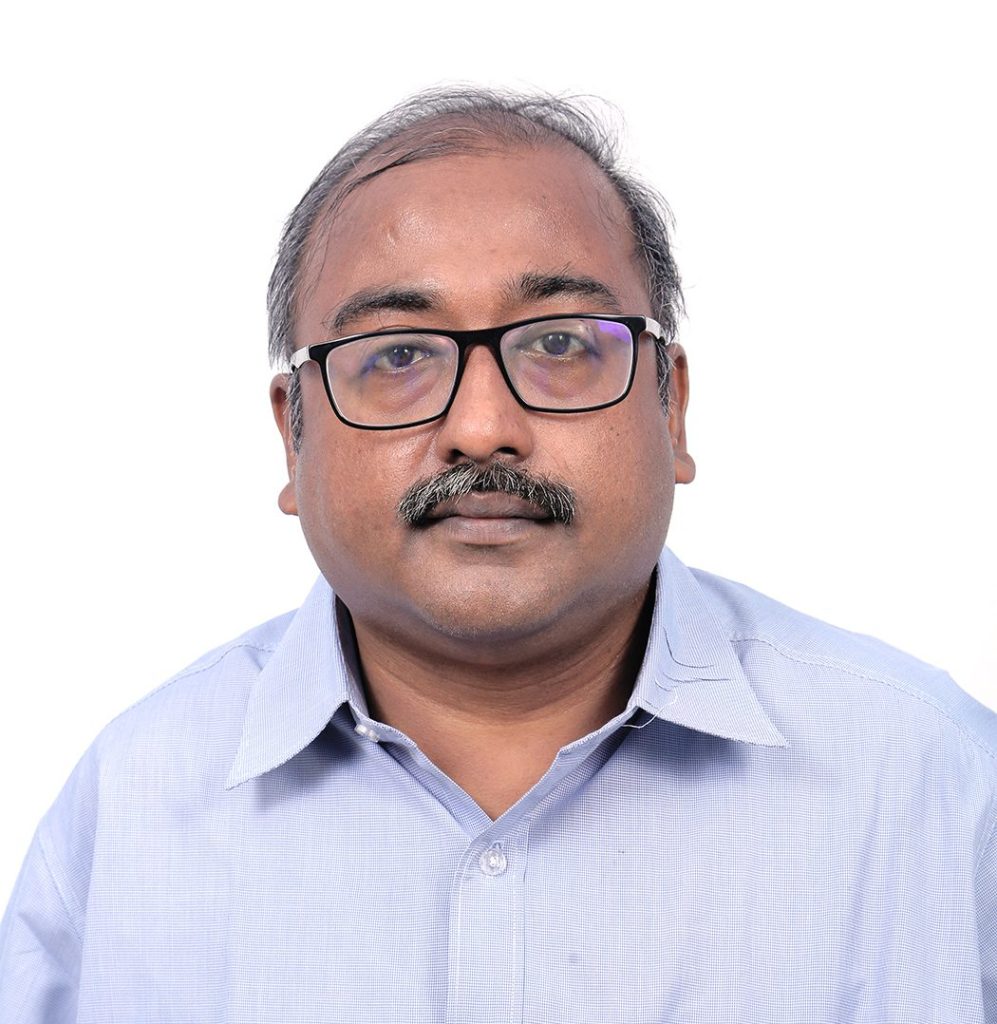
Kannan – GM – Application Engineering- LN, Hydrogen Power, Fertilizers, ASU & CCU
With 29 years of experience in the valve industry, Kannan’s knowledge expertise, and global awareness from working in multiple functions such as sales, application engineering, and project management have made him a respected figure in the Control Valve market with clients, earning him a reputation as a reliable and dynamic leader.
Kannan’s ability to anticipate market trends, build lasting relationships, and inspire his team is a testament to his unparalleled expertise and unwavering dedication to Severn, thus making him a valuable member of the IEW 2025 team.
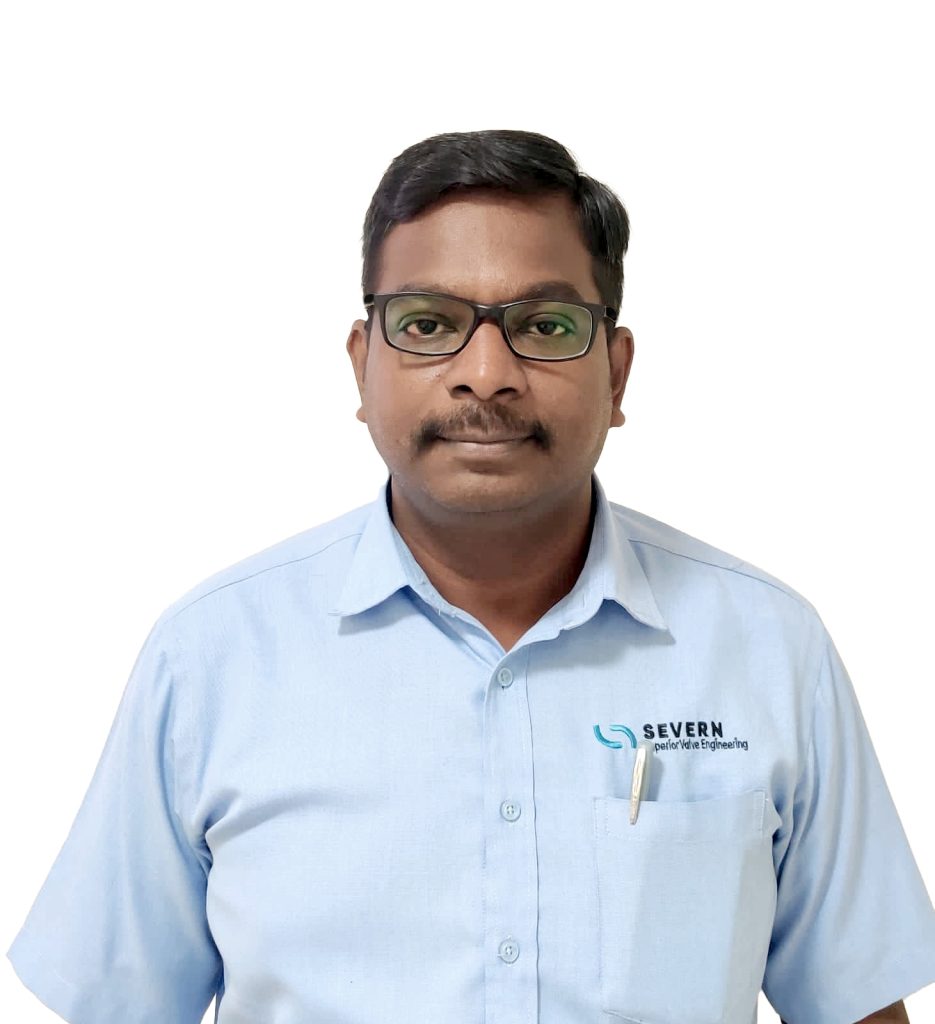
Rajendran – Industry Manager – Application Engineering – LNG & Industrial Gas
Rajendran is a key account manager, focussing on enhancing the customer experience with key customers.
With 20 years of experience in the field of Control Valve Application Engineering and Project management, he is in charge of business growth from key account customers of the Oil & Gas and Industrial Gas segments. He established credibility in handling small to large size Project & OEM orders from other industry segments such as Refining, Fertilizers, and Water.
He is into leveraging Severn’s strength with core customers by establishing frame agreements and driving projects for process improvements, value stream mapping, and lead time reduction.
He is further assigned to diversify the business in new geographical segments by posturing collaboration and value proposition. His expertise in Oxygen service and Cryogenic Valve applications supports customers in their emerging process control and automation requirements.
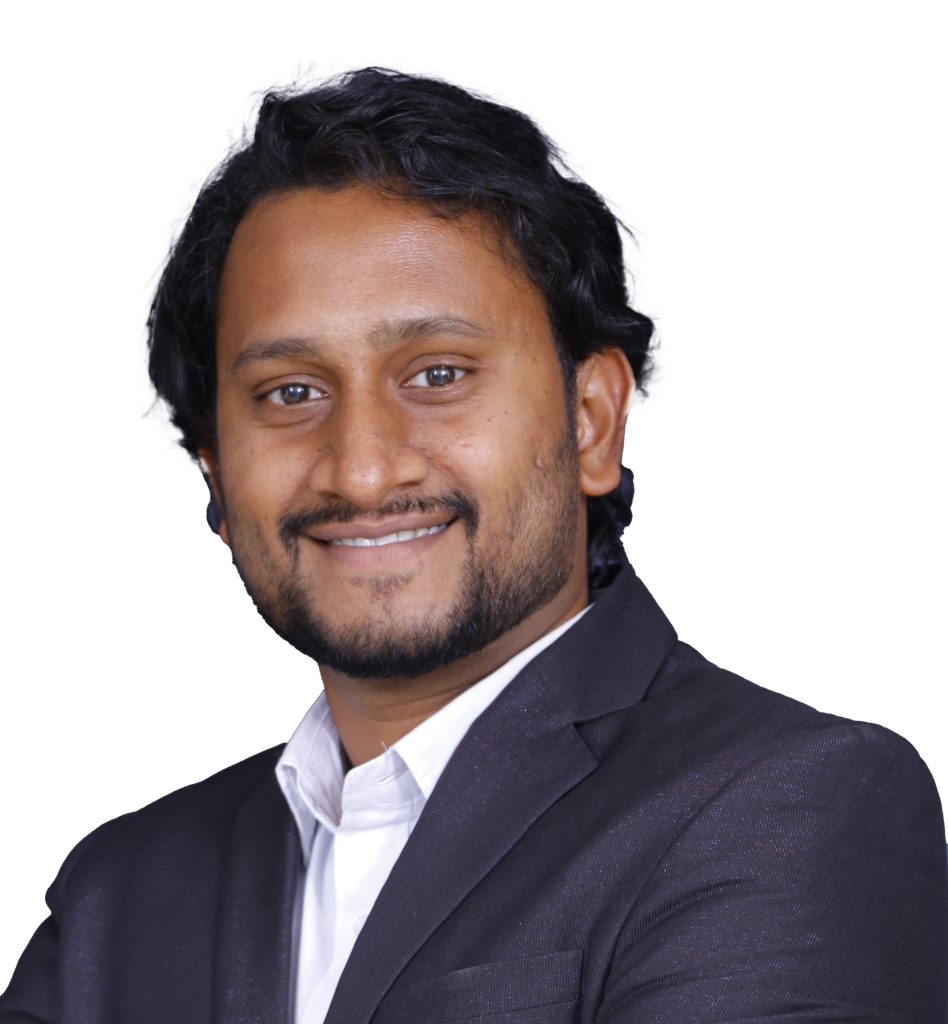
Chandru – Manager – Application Engineering – Oil & Gas, Onshore, Refinery & Petrochemical
A seasoned Control Valve professional with a decade of expertise in the Oil and Gas Industry (specialising in Oil & Gas – Onshore, Refinery & Petrochemicals).
Chandru excels in delivering optimised Control Valve solutions to our customers (EPC’s and OEM’s) and is recognised by our customers for 24×7 consultation on any unique challenges / services related to control valves in their projects.
Alongside technical expertise, Chandru is adept at identifying market trends, commercial aspects and customer pain points, translating these insights into customised Control Valve solutions that enhance customer satisfaction and expand Severn Products’ Global supply base.
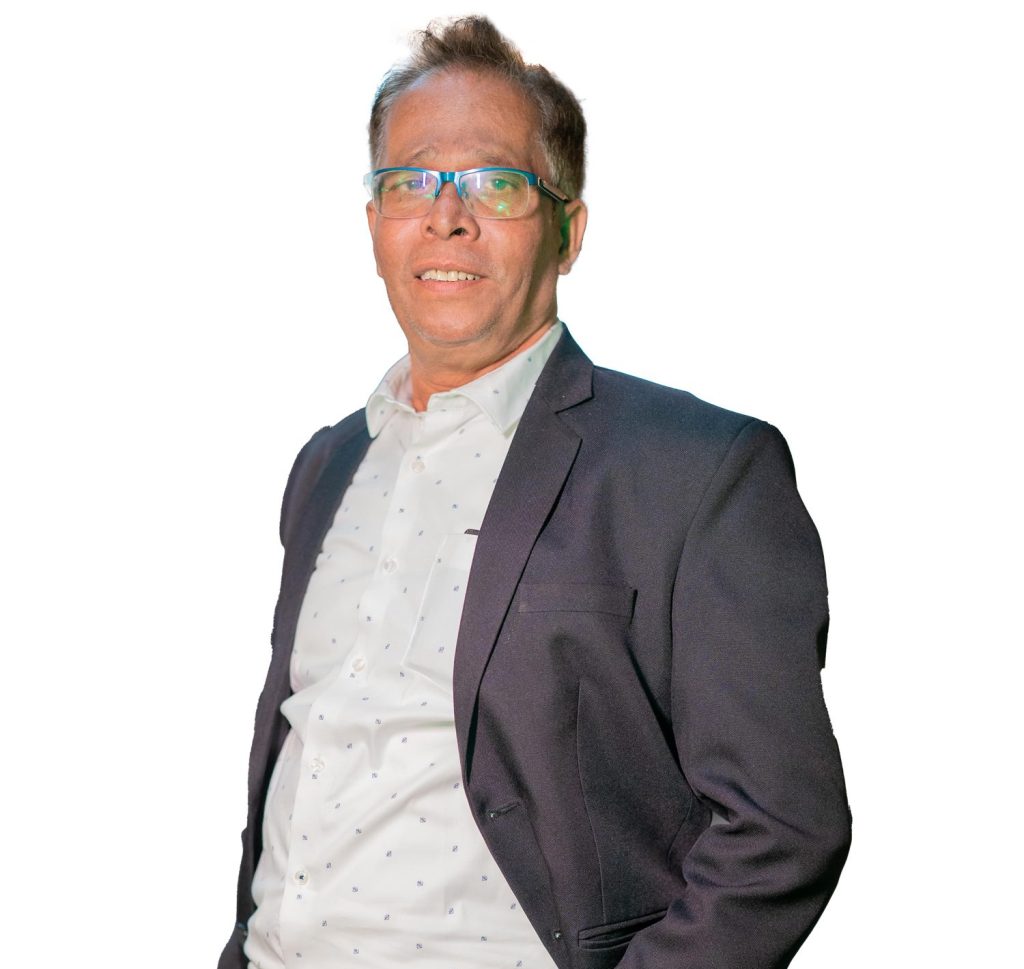
RK – Director – India Sales
RK joined Severn in 2017 as General Manager of Sales & Marketing to develop Domestic & Indian Subcontinent business.
With over 35 years total sales experience in process industries including Projects & MRO business, now as Sales Director of India region, RK identifies and captures new business opportunities with his strategic skillset and has delivered outstanding results, catapulting Severn to new heights in the Indian market.
With a proven track record of achievements in the Indian market, RK has become instrumental in driving revenue growth and expanding market share whilst forging lasting partnerships with clients and collaborators.
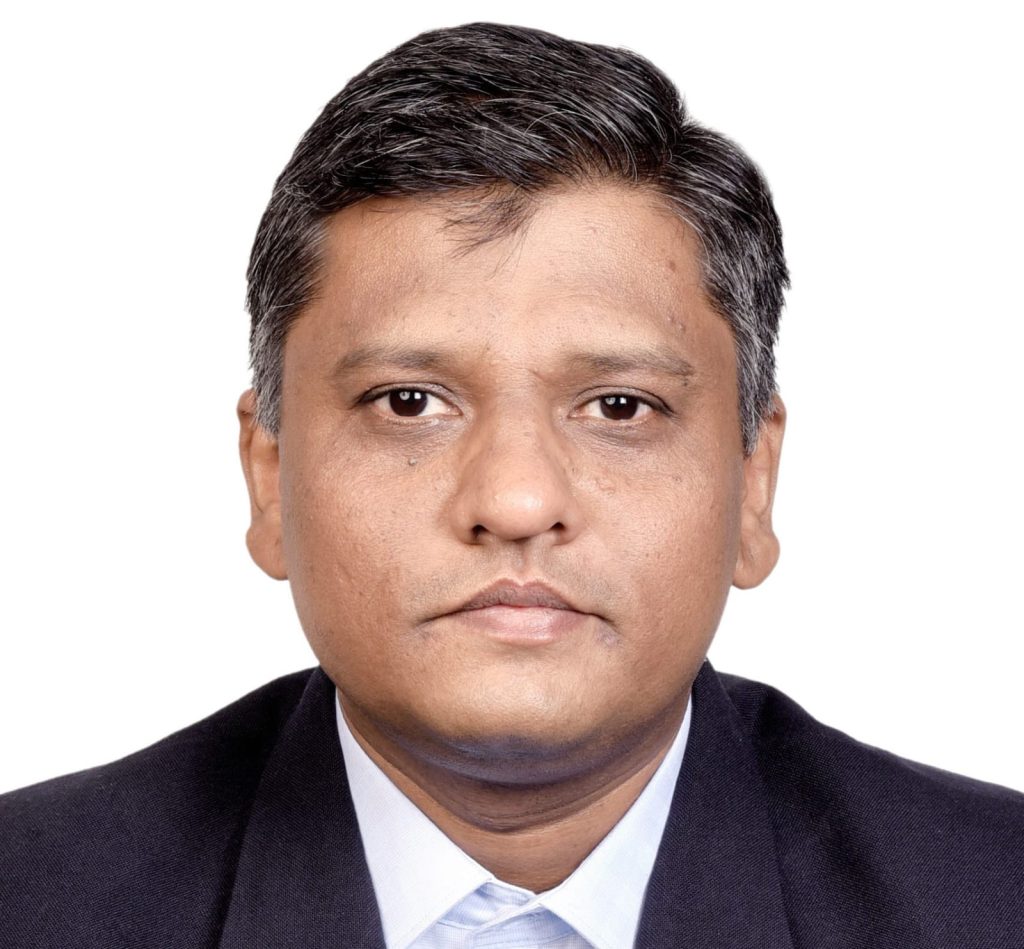
Gaurav – DGM – India Sales
Gaurav comes with a rich experience of two decades in the field of Sales & Business Development of Mission Critical Flow Control Products which play an important role in improving Process Efficiency, Uptime, Asset Management of an End User Process Plant together with Product Life-Cycle Management, New Market Developments thereby contributing to Organizations growth.
With Severn he is entrusted with developing the Project Business for our Severe Service Control Valves from Indian customers for both Domestic and International Projects through support of Field Sales Team with Severn’s values of Customer First, Integrity, Accountability & Excellence at the core of all the activities conducted.
Its our pleasure to invite you for a engaging discussion on business association, collaboration, emerging trends and flow control industry as a whole for a win-win relationship.
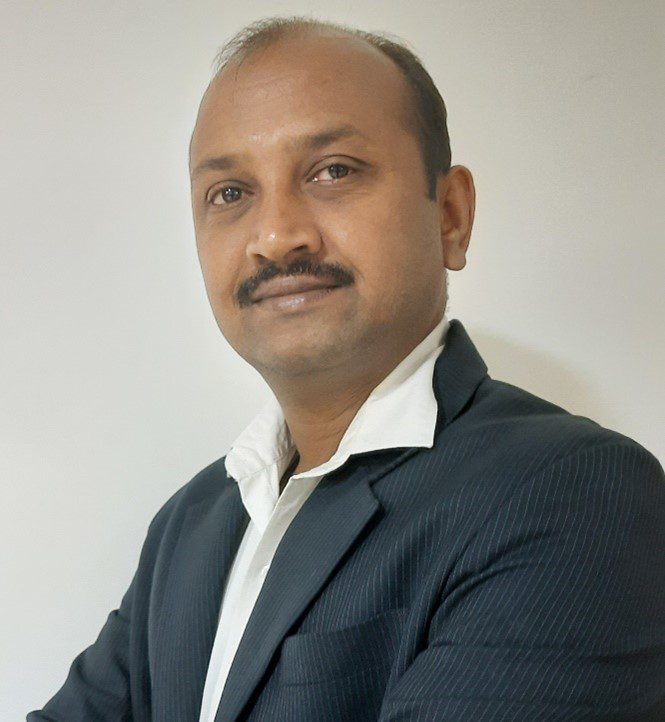
Sivakumar – Commercial Manager – MRO – Application Engineering
A seasoned leader in Valve Solutions bringing over 18+ years of experience in delivering top-tier solutions to industrial clients worldwide. My Journey in this field has been shaped by a strong foundation of technical expertise, customer-focused strategies, and innovative problem-solving. Comprehensive knowledge of valve industry processes systems, spares, and replacement strategies to optimize performance and reliability. Has a proven track record of diagnosing complex operational challenges and delivering efficient, cost-effective solutions. Deep understanding of client needs, ensuring tailored solutions that align with operational goals.
Leading a team committed to excellence in providing world-class on valves aftersales solutions. Our focus is on enhancing system performance, minimizing downtime, and ensuring our clients’ operations run seamlessly.
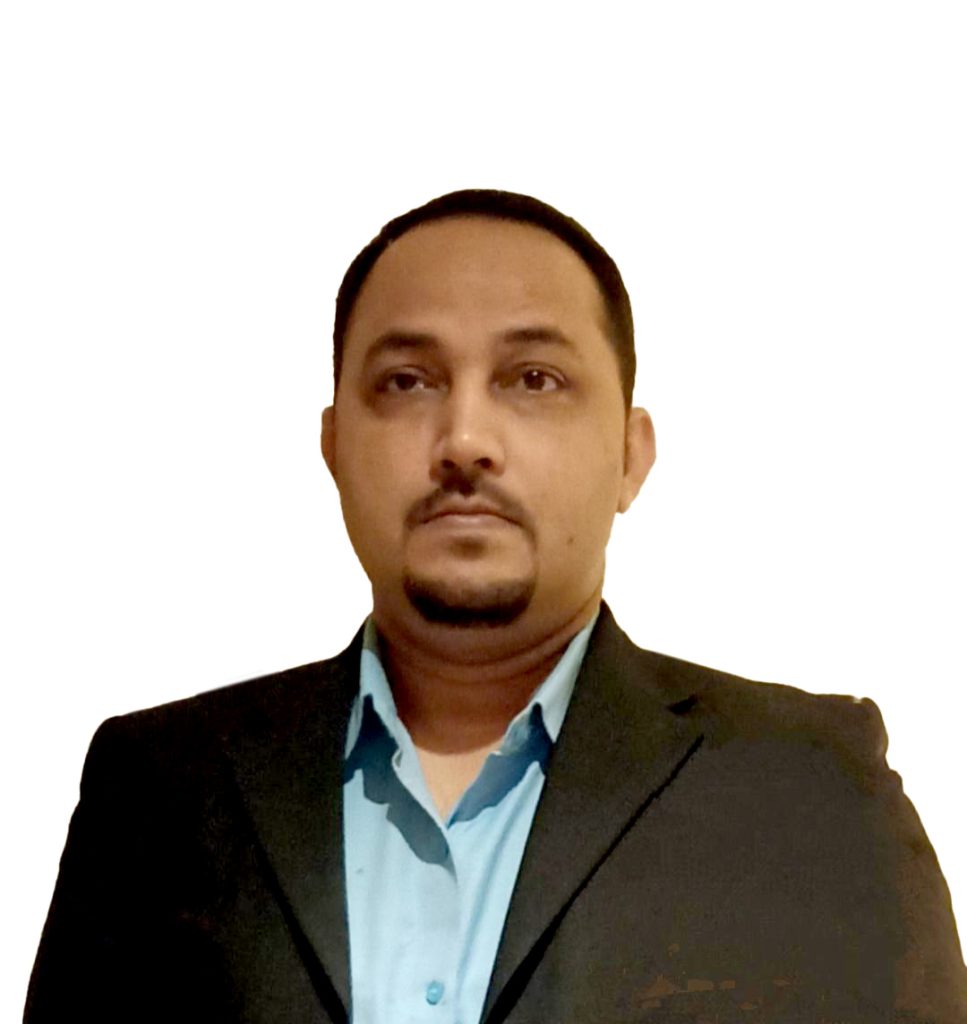
Sanjeev – Senior Manager – MRO – India Sales
With 17+ yrs of experience in Flow control industry, Sanjeev provides the techno-commercial expertise, clients relationship management, enhancing overall customer experience with after sales support, valves solutions for various customers within Oil & Gas Industry.
Sanjeev is overseeing MRO opportunities in India region, he is a trusted & well-versed with Severn’s core Control Valves products range & solution driven approach supporting end-customers to find solutions, enhance their efficiency, reliability and productivity, especially in severe services & challenging applications in process industries.